Our Services
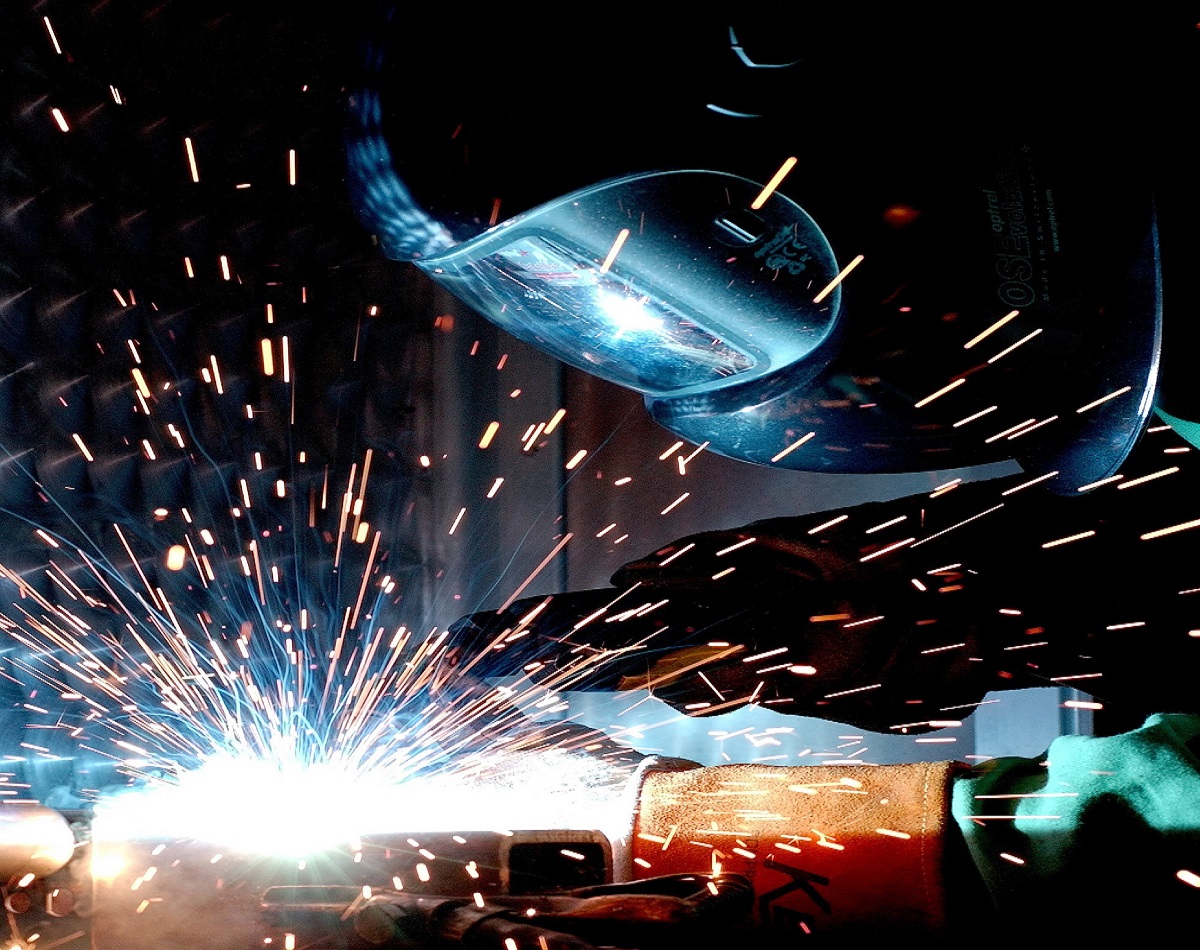
Special process Audits
A special process as per ISO 9000 is a process where its resulting output cannot be verified by subsequent monitoring or measurement. The ability to achieve planned results of such special processes needs to be validated and periodically revalidated. Automotive Industry Action Group (AIAG) has published a series of CQI standards (Continuous Quality Improvement) for the special processes which include:
- CQI 09 for Heat treatment
- CQI 11 for Plating
- CQI 12 for Coating
- CQI 15 for Welding
- CQI 17 for Soldering
- CQI 23 for Molding
- CQI 27 for Casting
QSC auditors are experts in your automotive industry and also certified to a range of automotive industry standards. Having worked with OEMs and throughout the automotive supply chain, our auditors can identify process cum operational issues and optimize process performances.

Supplier Audits
Supplier issues can cost organizations loads of money and most important result in customer rejections and dissatisfaction. As your business grows, so does the supplier base grow and so do the associated risks with each supplier. Every time you induct a new supplier you bring in risks of poor performance. Supplier audits are the most effective way to evaluate and select suppliers without letting in those risks and preventing the issues from turning into bigger problems. Supplier audits help you verify if the supplier’s quality systems, processes or products meet your requirements as defined in your contractual agreements and/or agreed standards.
Organizations mostly have difficulties in the covering the audits of the entire supplier base and often lack the technical process and product knowledge.
QSC can help you manage your supply chain efficiently by auditing your suppliers to identify potential risks, gauge compliance to your business requirements, uncover potential gaps in their quality and manufacturing processes and moreover align them with your business goals.
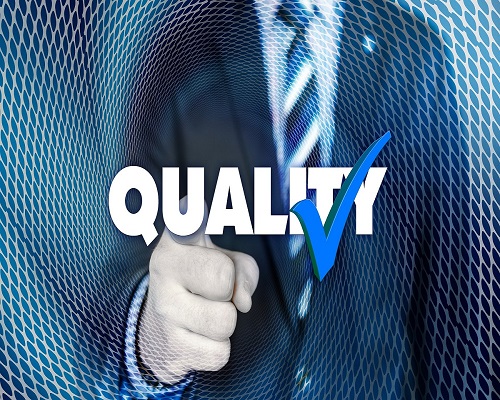
Process/Product Audits
Process audits help verify whether processes are performing well within specified controls and established limits. A process audit may check adherence to defined process parameters like time, temperature, speed, pressure, chemical composition, responsiveness, composition of any mix, service and transaction outcomes. It can further help to establish the adequacy, effectiveness and efficiency of the defined process specifications within the standard operation procedures, quality plans, test plans, control plans etc.
Product audit are an inspection of a final product / service before delivering it to a supplier or a customer. It often extends to assessing the packaging specifications and shipment requirements including transportation and preservation requirements. Product audit is an examination of a particular product or service, such as hardware, processed material, or software, to evaluate whether it conforms to requirements (i.e., specifications, engineering drawings, performance standards, and customer requirements. It is often referred to as a quality audit.
QSC’s process/product auditors have a varied and rich experience in almost all manufacturing processes, products and services. Being well versed with the technical requirements of the process and product including associated risks and customer requirements they can help accelerate your performance.
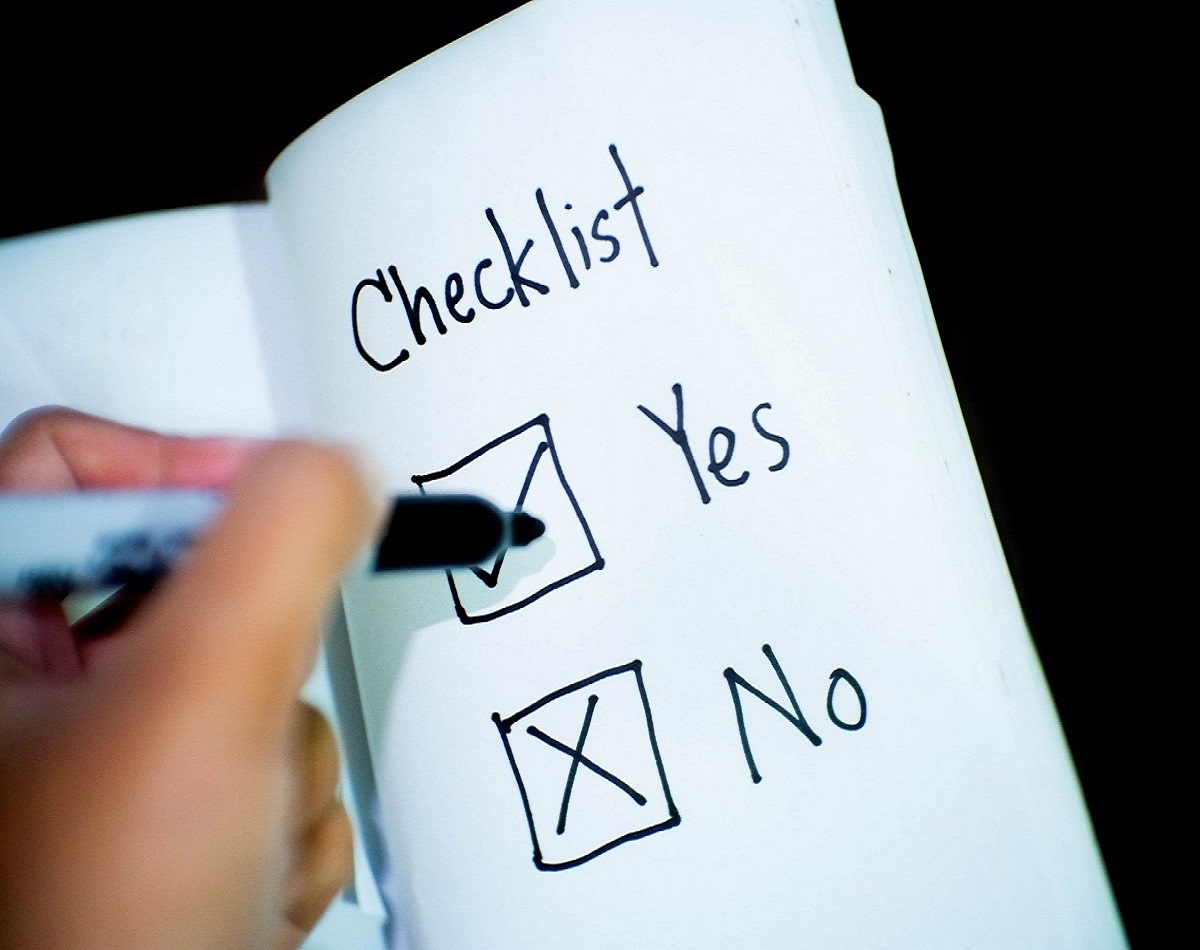
Internal Audit
An internal audit is a vital component to ensure optimal performance of your management systems, be it Quality, Environment, Health, Safety, Information Security, Aerospace, Automotive or any management systems. The role of an internal audit is also to provide independent assurance that an organisation’s risk management, governance and internal control processes are operating effectively. Internal audits can also assist in monitoring the defined system and checking applicable legal requirements are complied to including customer requirements. Typically, there are four phases in any internal audit – planning, conducting, reporting and follow up as required by ISO 19011.
QSC auditors are trained, qualified and certified in all the management systems including requirements of ISO 19011. We help you plan your audits, conduct value added audits using standard specific prescriptive audit checklists and provide a detailed report on the overall conformances, risks or weakness that exist in your processes, areas of improvement and non-conformances if any.
QSC always strives to provide the best training courses including course materials and certifications that are specific to your industry and all levels of operations. Course materials are prepared and continually updated by highly experienced industry experts for professionals of all experience and skill levels. Courses are taught by industry experts having a rich industry and teaching experience that let organizations and individuals gain and apply the knowledge and skills acquired in our trainings.
QSC offers operational excellence courses that helps employees achieve self-sufficiency, cost savings, decreased repair and rework and increased ROI. Our management systems courses help organizations and process owners understand what the requirements of the management systems are, how to implement and establish the management system requirements, how to audit and continually improve the established management systems.
QSC with its extensive training experience can also work with your organization to provide Bespoke Training Courses. Our training experts understand your training needs, build and help deploy training solutions that bring tangible business benefits.
Call 9850576267 or write to us info@qualsiddh.com for your bespoke training needs.
QSC offers and conducts :
- Public courses
- On-site courses
- Virtual (On-line training)
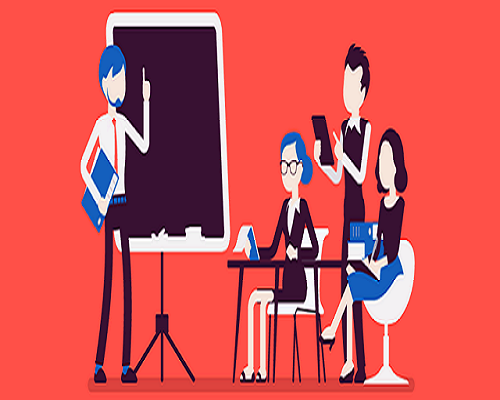
Operational Excellence Courses
- 7 QC tools
- 5S / 7S
- Kaizen
- Problem Solving Techniques
- Effective Root Cause Analysis
- APQP & Control Plan
- PPAP
- FMEA
- MSA
- SPC
- 8D Methodology
- AIAG CQI series
- Risk Management
- EMS Aspect Impact Identification
- OHS Hazard & Risk Assessment
- First Aid
- Fire-fighting
- ISMS Vulnerability Assessments
- ISMS Penetration Testing
- Implementing ISMS policies
& controls and many more…
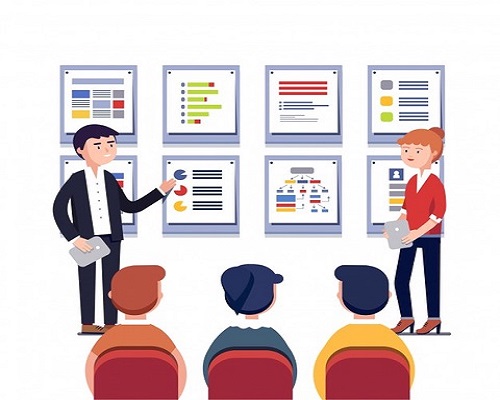
Management System Courses
- 1 Day – Awareness Course – For individuals who wish to gain basic knowledge of the relevant standard.
- 2 Day – Foundation Course – For individuals who wish to gain detailed knowledge of the relevant standard & its requirements
- 3 Day – Internal Auditor Courses – For individuals who wish to become internal auditors and audit their organizations processes.
- 5 Day – Lead Auditor Courses – For individuals who wish to conduct third party audits of the relevant standard & its requirements.
- 5 Day – Lead Practitioner Courses – For individuals who are responsible to establish, implement and manage the relevant standard in their organizations.
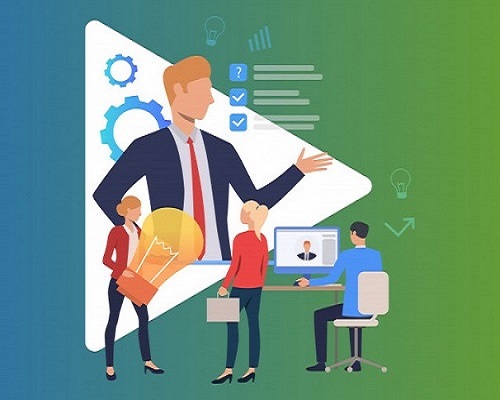
Virtual (on-line) Courses
Short of budget? Schedule Flexibility? Not much time to travel?
Try our Virtual Training courses. Our trainers although away from your workplace, create a conducive classroom atmosphere, increased participation and engagement with your other fellow learners and a great learning experience.
Call us on 9850576267
Email us at info@qualsiddh.com to know more about our virtual training courses.
QSC consultants have an average working experience of 25 years in manufacturing, service and IT sector. Our consultants understand your requirements, carry out an as-is mapping of your business processes,identify areas of improvement, facilitate process definitions, conduct counselling sessions in implementing processes and help businesses achieve excellence and customer satisfaction.
QSC also provides similar end-to-end consultancy services to help its customers achieve third party certifications to various ISO management system standards or continual improvement in your existing business practices.
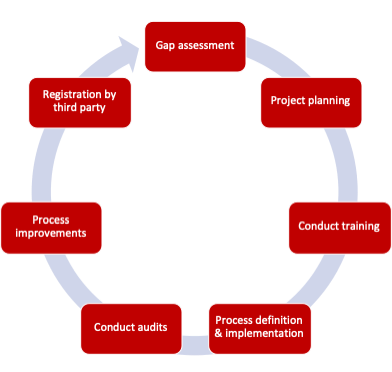
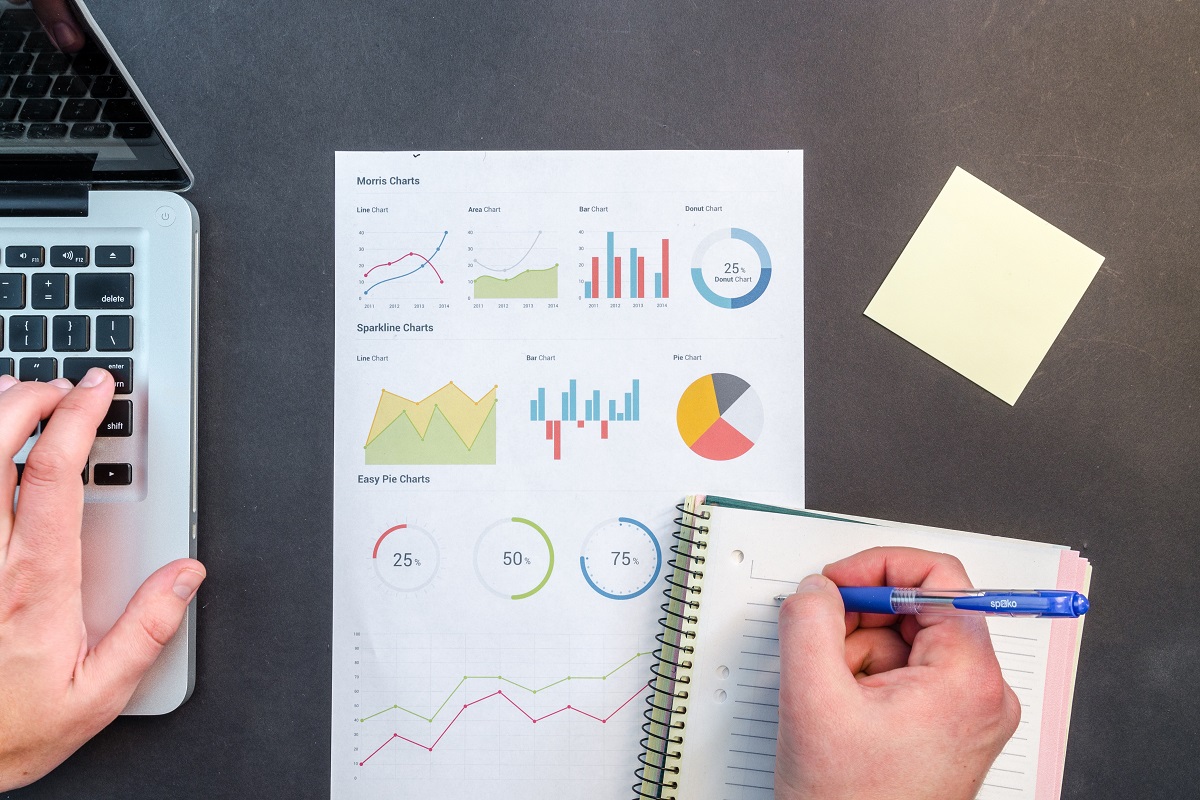
ISO 9001
ISO 9001 is defined as the international standard that specifies requirements for a quality management system (QMS).
Organizations use the standard to demonstrate the ability to consistently provide products and services that meet customer and regulatory requirements.
Being ISO 9001 certified is well worth the effort and time put into it.
Not only will your organization be more efficient and quality-driven, but your employees and customers will also see a significant, positive difference!
QSC helps its customers establish a quality management system (QMS) ensuring that the entire organization works together towards the continuous improvement of the processes, products, workflows, and culture to meet customer expectations, it’s applicable legal requirements and attain business goals in a streamlined manner.
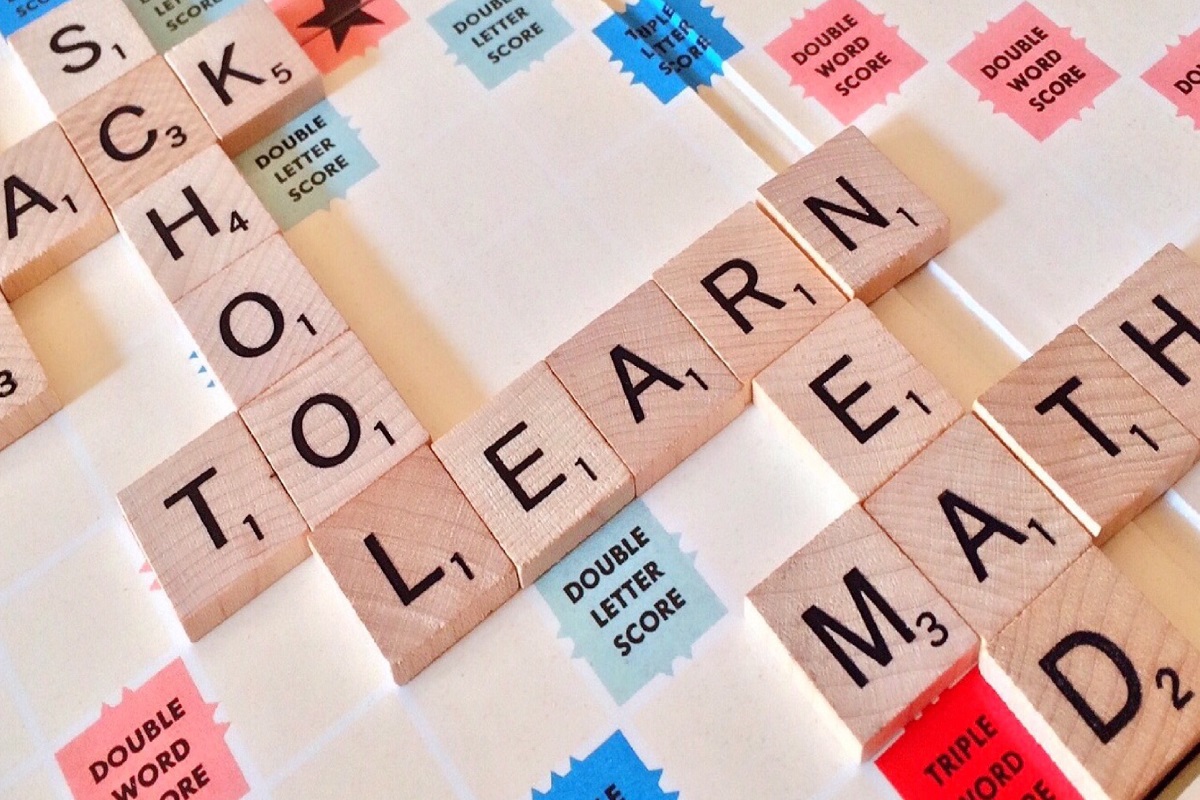
ISO 21001
The new ISO management system standard for educational organizations (EOMS).
ISO 21001 is the newly published standard recently in 2018 and is now the preferred standard for educational institutes / organizations. Educational organizations include pre-school, primary, elementary, middle schools, high schools, colleges, universities, adult education, vocational education and training, tutoring or coaching centers, training organizations.
ISO 21001 – EOMS is intended to provide a common management tool for organizations providing educational products and services capable of meeting learner and other customer requirements and needs.
QSC till date has helped many business management, catering and technical institutes in establishing and educational management systems and getting them certified by an accredited third-party registrar.
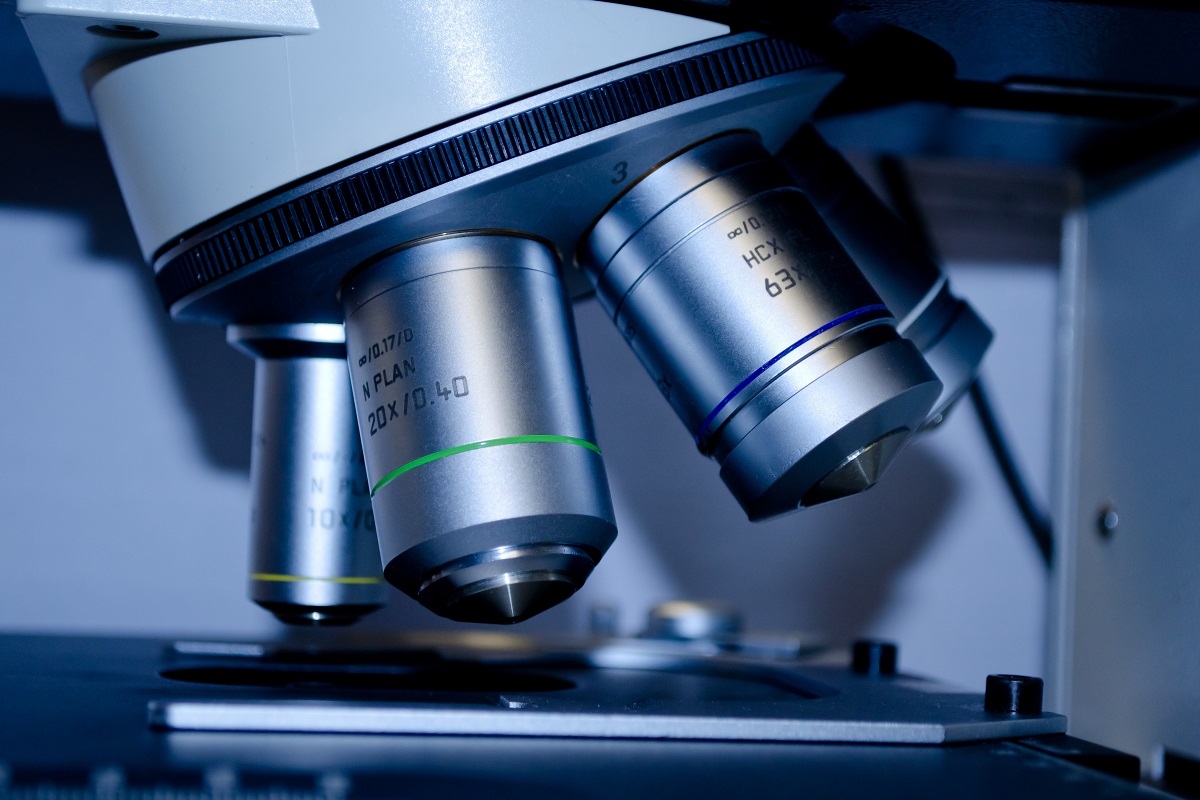
ISO 13485
This internationally agreed standard sets out the requirements for a quality management system specific to the medical devices industry.
A medical device is a product, such as an instrument, machine, implant or in vitro reagent, that is intended for use in the diagnosis, prevention and treatment of diseases or other medical conditions.
ISO 13485 is designed to be used by organizations involved in the design, production, installation and servicing of medical devices and related services.
ISO 13485 firmly ensures the use of best practices throughout all steps of a medical device’s life cycle.
Most importantly serves as a regulatory & legal requirement in many countries.
QSC experts will offer you a qualitative experience ensuring your requirements are met.
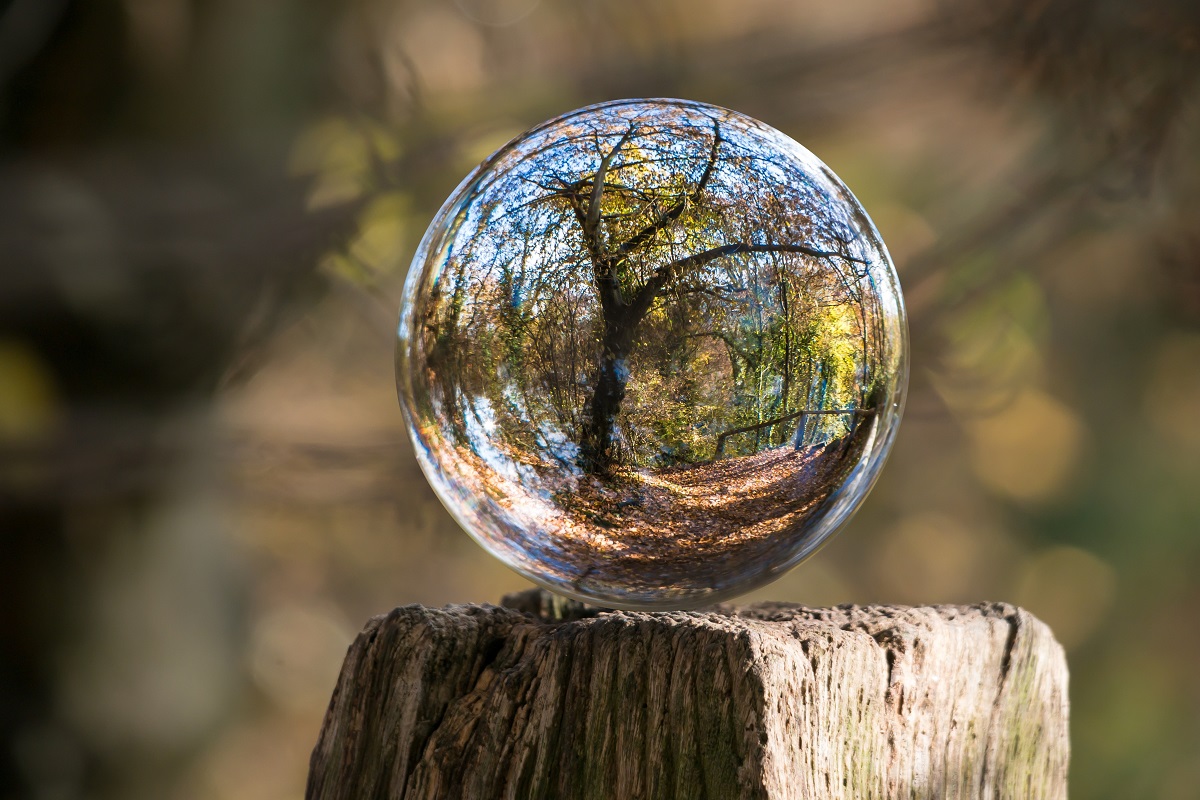
ISO 14001
ISO 14001 is the most widely used Environmental Management System (EMS) standard in the world that helps you to control your environmental aspects, reduce impacts and ensure legal compliance.
Designed for any type of organization, regardless of its activity or sector, it can provide assurance to company management and employees as well as external stakeholders that environmental impact is being measured and improved.
Issues including air pollution, land and groundwater contamination, disposal of hazardous wastes and E-waste are the main concerns of governments, industries and customers.
QSC’s environmental experts help you to establish and implement an EMS which not only improves your environmental performance but grow your business in a sustainable manner.
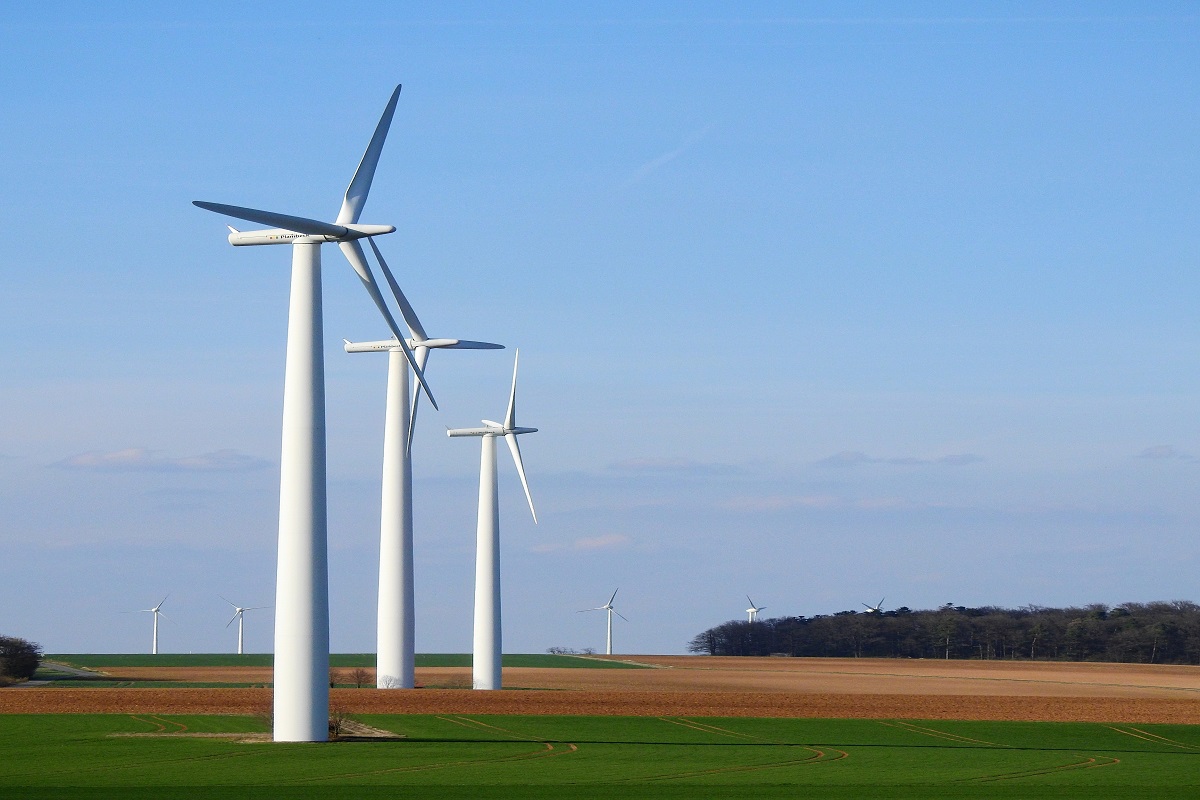
ISO 50001
ISO 50001 specifies Energy Management Systems (EnMS) requirements for any organization looking at reducing energy consumption and improving energy efficiency.
It enables organizations to establish the systems and processes necessary to continually improve energy performance, energy use and energy consumption.
Energy often is the highest operating cost for any organization.
By improving energy performance and associated energy costs, organizations can be more competitive.
In addition, implementation can lead organizations to meet overall climate change mitigation goals by reducing their energy-related greenhouse gas emissions.
QSC helps organizations to realize untapped energy efficiency potential.
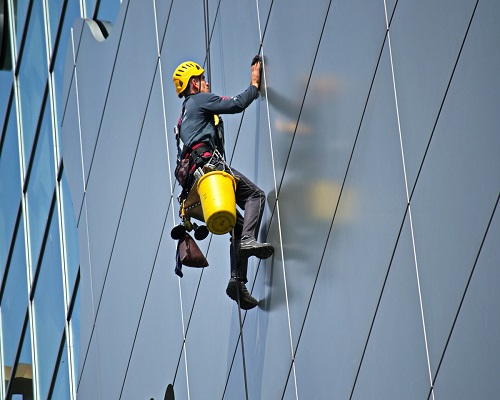
ISO 45001
ISO 45001 is the newly developed international standard for Occupational Health & Safety (OHS) Management System and replaces OHSAS 18001.
Globally across all industries there are nearly 7500 plus incidents/accidents or diseases per day which is one of the prime reasons why health and safety is the number one priority of all businesses.Irrespective of the type of business / industry you are in, accidents that lead to injury or health related issues are always likely to occur.
Just like all other ISO standards, ISO 45001 too is applicable to all organizations, regardless of size, industry or nature of business.It requires that organizations integrate the OHS requirements into their existing business processes in order that organizations can increase their OHS performance.
Our safety experts enable organizations bring in place an OHS management system that helps manage OH&S hazards & risks and reduce workplace incidents leading to a healthy & safe work culture.
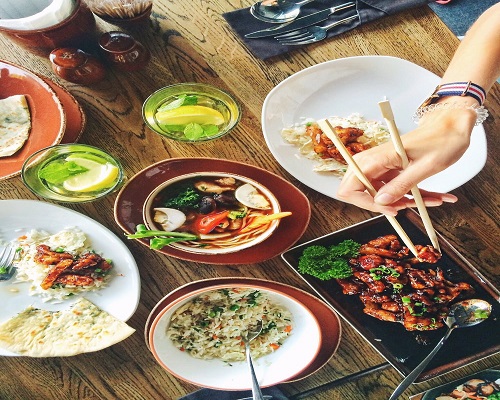
ISO 22000
A foodborne illness is a disease transmitted by food to people. Every year lakhs of people fall sick from unsafe food. A food safety management system can prevent these kinds of outbreaks and save a company thousands of rupees. ISO 22000 also referred to as Food Safety Management Systems (FSMS) is a sector specific standard that describes a specific process to direct and control food safety aspects. It helps the food business operators to gain this trust of the consumers or even serve them efficiently. ISO 22000 can also ensure regulatory compliance to ISO standards by actively controlling risks and hazards throughout the food process. Once identified, these hazards can be prevented, eliminated, or reduced to safe levels.
QSC can help your company implement an effective FSMS keeping both your business and the public safe from foodborne illnesses.
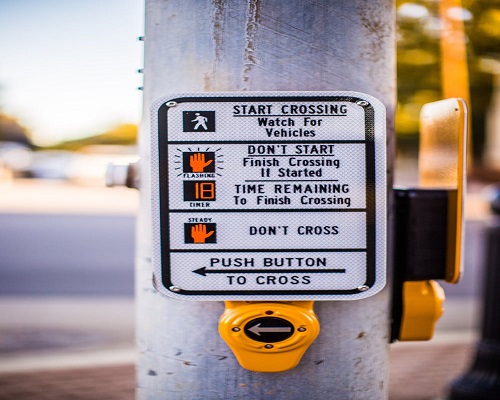
ISO 39001
ISO 39001 – Road Traffic Management Systems (RTSMS) specifies requirements for any organization, public and private, that interacts with road safety systems. Every minute someone is killed in a road accident and claims a life of a near and dear one within a family.The ultimate goal of the RTSMS is to eliminate road fatalities and serious injuries associated with road traffic accidents.
Implementing ISO 39001 helps contribute to the national and global efforts to prevent fatalities and injuries in road crashes and demonstrate organizations commitment to issues that can be of public concern.
QSC can help organizations set up road traffic processes needed for safer mobility, identify RTS performance factors and improve RTS performance.
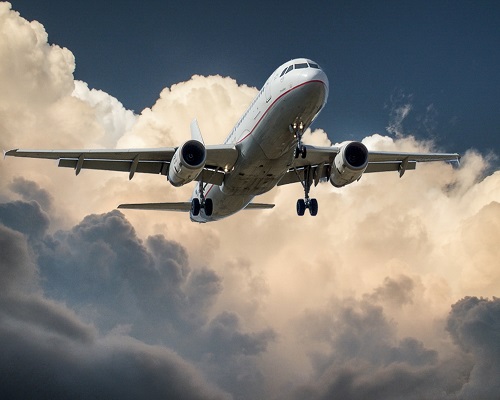
AS9100
AS9100 is the international Quality Management System standard for the Aviation, Space and Defense (AS&D) industry, created by the International Aerospace Quality Group (IAQG). AS9100 was established with the primary aim of providing safe and reliable products for the aerospace industry.
It is used and supported by the world’s leading aerospace companies and throughout their supply chains.
This standard is intended for use by organizations that design, develop, or provide aviation, space, and defense products and services.The Aviation Industry is highly regulated with demands and controls that ensure the safety and reliability of equipment and materials.
The industry relies heavily on suppliers demonstrating effective management systems.
AS 9100 sets the quality levels expected in all areas of aerospace, from commercial to defense aviation.
QSC helps organizations develop Aerospace QMS ensuring your internal processes improve and achieve customer expectations.
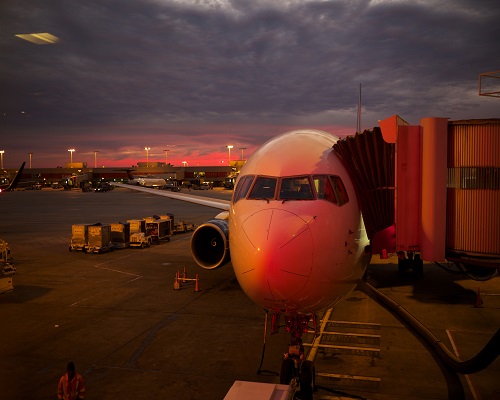
AS9110
AS9110 is a standard intended for use by organizations whose primary business is providing maintenance or continuing airworthiness management services for civil or military aviation articles and products and by original equipment manufacturers with maintenance, repair, and overhaul operations that are operated autonomously, or that are substantially different from their production operations.A standard supported by International Aerospace Quality Group (IAQG) is based on AS9100 and adds specific requirements that are critical for the Maintenance, Repair & Overhaul (MRO) of commercial, private, and military aircrafts.
QSC helps organizations develop management systems which meet these requirements and achieve registration to AS9110.
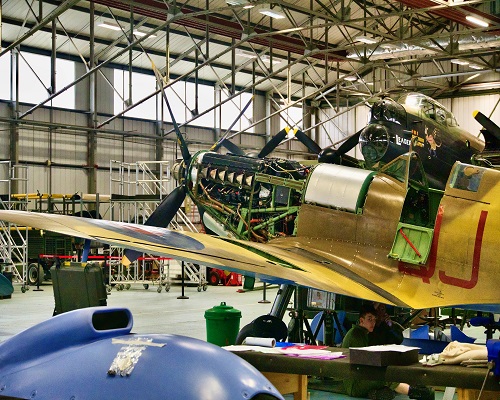
AS9120
AS9120 – Quality Management Systems – Aerospace Requirements for Stockist Distributors – was developed for stockist or pass-through distributors of aerospace commodity items.
Society of Automotive Engineers (SAE) manages this standard which is regulated by the IAQG (International Aerospace Quality Group).This standard is part of the AS9100 series and addresses chain of custody, traceability, control and availability of records of companies that procure parts, materials and assemblies and sells these products to a customer in the aviation, space and defense industries.
This includes organizations that procure products and split them into smaller quantities.
The standard would be applicable for organizations that resell, distribute, and warehouse parts found in aircraft and other aerospace components.
QSC works towards aligning your operations to meet these requirements for inventory control, lot tracing, and vendor management, ensuring consistency throughout their supply chain.

IATF 16949
IATF 16949 developed by the International Automotive Task Force (IATF) with support from Automotive Industry Action Group (AIAG), is a global Quality Management System Standard for the Automotive industry.IATF 16949:2016 incorporates the structure and requirements of the ISO 9001:2015 quality management system standard with additional automotive customer-specific requirements. The standard applies to all manufacturers in the automotive supply chain worldwide – for cars, their parts, components or systems. Certification to this technical specification provides global recognition for suppliers sourcing across the automotive industry.
Some of the vital key focus areas of IATF 16949 includes continual improvement, defect prevention, reducing waste, product safety & above all risk management.
QSC has experienced automotive industry experts who will help you make continuous improvements to your systems and process quality and place customer-specific requirements at the heart of what you do.
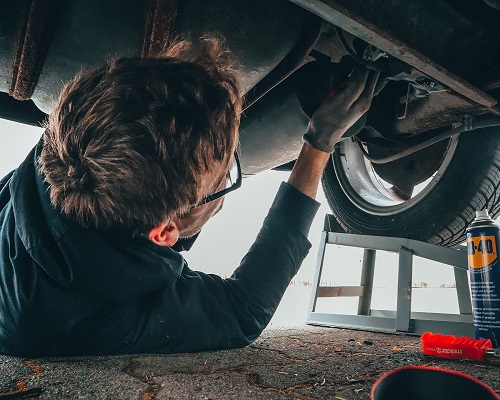
VDA 6.3
VDA is the German abbreviation for the “Association of the Automotive Industry” (Verband der Automobilindustrie e.V.). Developed by VDA QMC and the German automotive industry, VDA 6.3 defines a process based audit standard for evaluating and improving controls in a manufacturing organization’s processes. This association publishes guidelines for the automotive industry for the implementation of standards and the realization of OEM requirements. The standard can be used by any organization, either for internal process audits, or for evaluating potential or existing suppliers. The standard can also be used by any organization, either for internal process audits, or for evaluating potential or existing suppliers. Compliance to VDA 6.3 is mandated by some vehicle makers and encouraged by others.
QSC experts are qualified and certified by VDA-QMC and can help deploy these German automotive requirements.
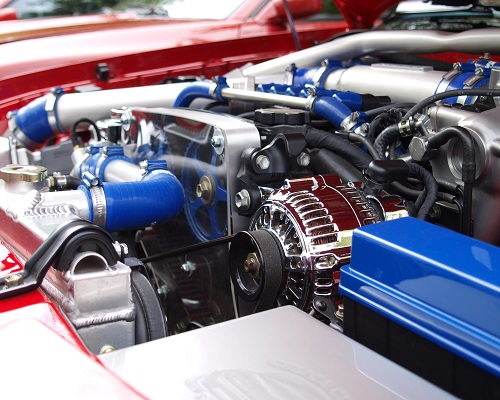
A- SPICE
A-SPICE stands for Automotive Software Process Improvement and Capability dEtermination. It is yet another standard developed by the German Automotive Industry. Automotive projects are getting more complex by the day and the focus has changed from mechanical challenges to more software’s in the car.Expectations of the customer in terms of comfort, infotainment and safety are also increasing requiring automobile manufacturers to change their development process and moreover shorten the life cycle of their software projects. A-SPICE is an internationally accepted process model that defines best practices for software and embedded systems development for the automotive industry.
QSC consultants are qualified to conduct software life cycle audits and with the automotive manufacturing background are competent to help clients establish a process maturity framework thereby improving the automotive software development processes.
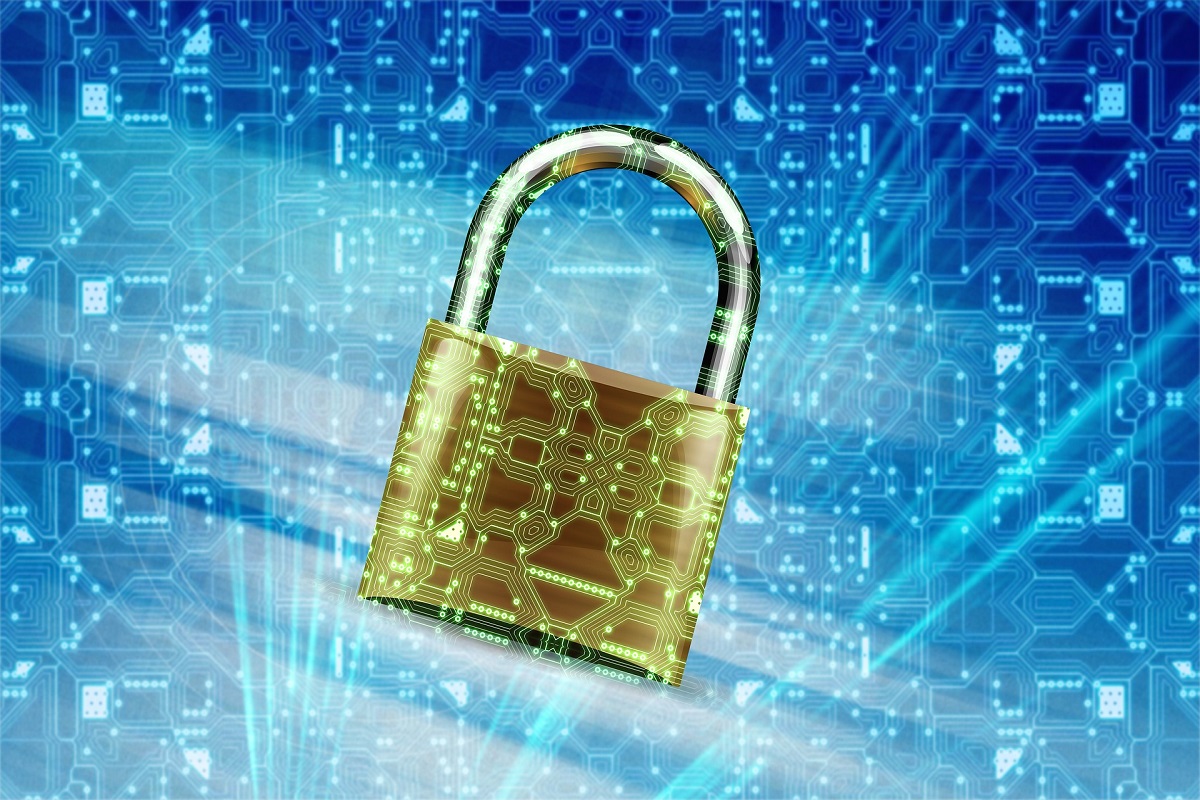
ISO 27001
Keeping information assets secure, be it financial, intellectual, employee related or managed by third parties, it has become crucial to all organizations and ISO 27001 is the most widely used and preferred standard that sets out the requirements for an Information Security Management Systems (ISMS).The standard covers all types of organizations from micro-businesses to huge multinationals, and all sectors like retail, banking, defense, healthcare, education and government. ISO 27001 works on three security goals Confidentiality, Integrity & Availability. ISO 27001 draws coordination between all sections of an organization and a framework of policies and procedures that includes all legal, physical and technical controls involved in an organization’s information risk management processes.
QSC experts assess the information risks that exist in your organization, identify applicable controls and help evolve an ISMS that continually improves the safety of your information.

CMMI
CMMI – Capability Maturity Model Integration as it stands for was developed by the Software Engineering Institute at Carnegie Mellon University as a process improvement tool for projects, divisions or organizations. The DoD and U.S. Government helped develop the CMMI, which is a common requirement for DoD and U.S. Government software development contracts. The CMMI is currently administered by the CMMI Institute, which was purchased by the ISACA in 2016.The Capability Maturity Model Integration (CMMI) helps organizations streamline process improvement, encouraging a productive, efficient culture that decreases risks in software, product and service development. CMMI defines the following maturity levels for processes: Initial, Managed, Defined, Quantitatively Managed, and Optimizing.
QSC’s CMMI consultants can help you successfully upgrade to the new CMMI 2.0 model or to a new implementation.
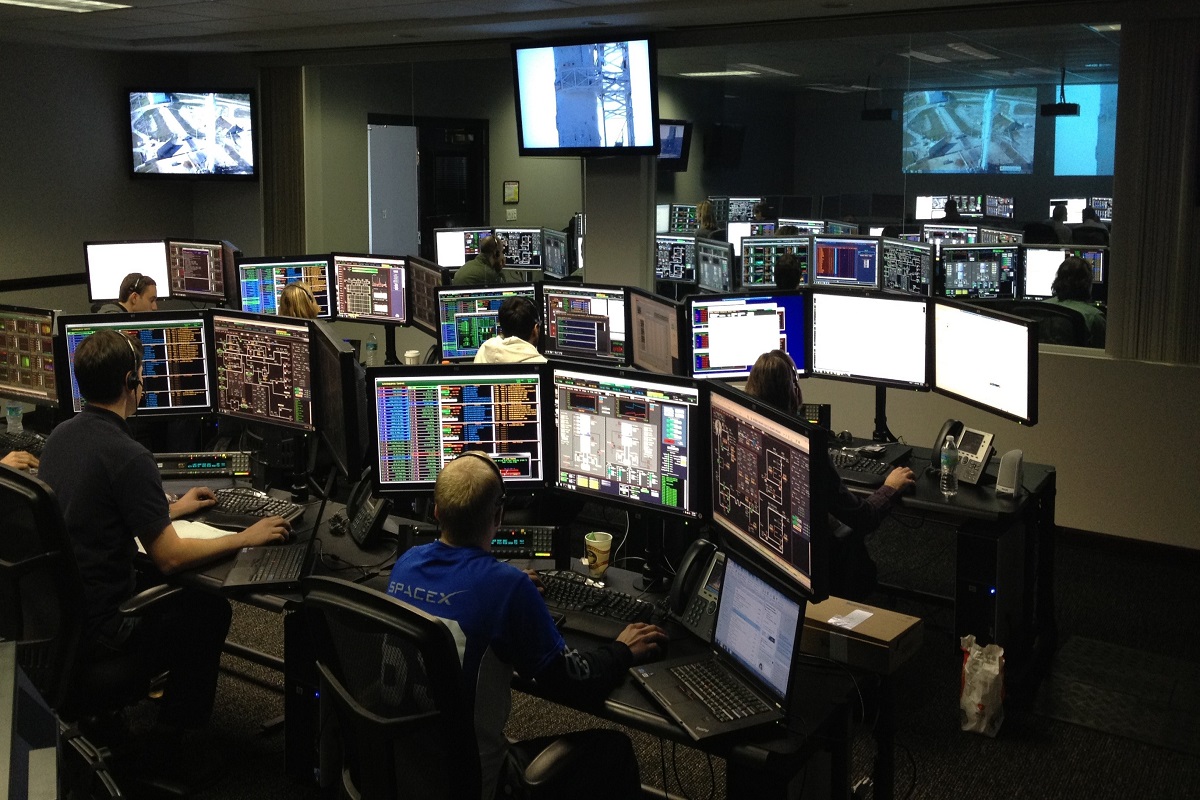
ISO 20000
ISO/IEC 20000 is the first internationally acknowledged standard for service management. It was developed in 2005 based on the earlier BS 15000, and subsequently revised in 2011 and 2018.
This standard specifies requirements for an organization to establish, implement, maintain and continually improve a service management system (SMS). The requirements specified include the planning, design, transition, delivery and improvement of services to meet the service requirements and deliver value.ISO 20000 certification confirms that an organization is conscious about their customers service deliverables, committed to service quality, has implemented number of IT controls that ensures fulfilment of IT Service Level Agreements, and IT availability risks.
QSC builds your skills and helps your organization become a competitive differentiator for the delivery of services.
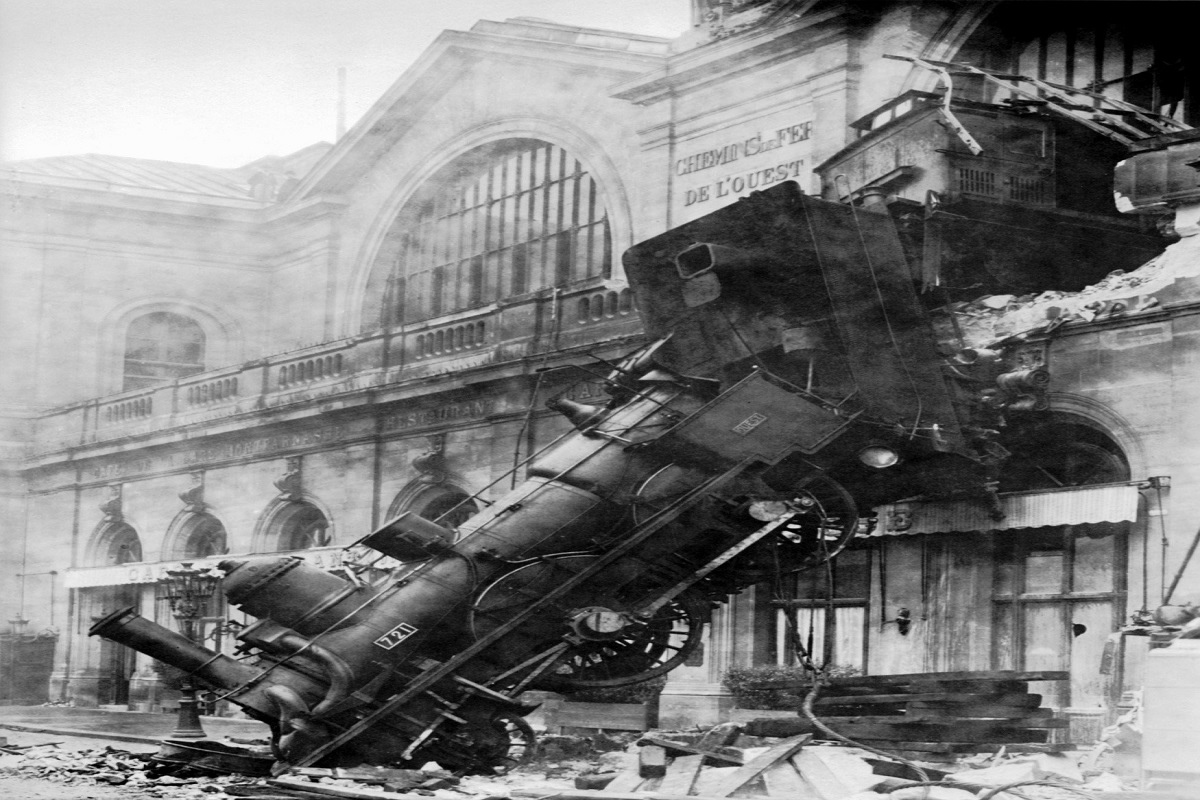
ISO 22301
ISO 22301 provides a framework to plan, establish, implement, operate, monitor, review, maintain and continually improve a business continuity management system (BCMS). It is expected to help organizations protect against, prepare for, respond to, and recover when disruptive incidents arise. Implementing a BCMS within your organization means that you are prepared for the unexpected. It helps you to manage risks to handle the threat of business activities or processes being interrupted by external and/or internal factors.Winning new business contracts, protecting revenue and profits, optimal recovery from a damaging incident, and compliance with regulatory requirements are all benefits of an ISO 22301-aligned BCMS.
QSC can help assessing your current business continuity arrangements against the Standard and provide you with a roadmap to implement an effective BCMS.
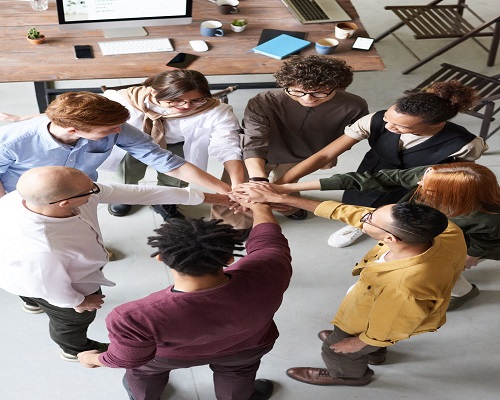
Supplier Development
Suppliers have a pivotal role at every stage of the product lifecycle. The role of a supplier in a business is to provide high-quality products. From sourcing raw materials to helping ramp up production, and to finding better options for raw materials as the market starts becoming saturated, companies need to work closely with their suppliers to get the best out of their products. Supplier development programs need to be a major focus of organizations who manufacture products and have a supply base because they lead to better overall relationships with suppliers and will improve communication, quality, and delivery as a result. Developing suppliers of vital goods and services can result in lower cost, improved quality and consistent on-time delivery.
QSC works with your identified suppliers on a one-to-one basis to improve their performance and ability to deliver goods or services that will satisfy your customers’ needs. Be it implementing any ISO management systems or PPAP implementation and submissions, following your own corporate policies, your Supplier Management Systems or conducting supplier audits to ensure your legal and process/product/customer requirements are met at all times, our consultants work collaboratively with your suppliers to boost their performance.
“Simply put, Lean Management Systems (LMS) means creating more value for customers with fewer resources.” Used originally by manufacturing organizations, LMS is a performance-based, continuous-improvement strategy that focuses on eliminating waste and unnecessary steps in company processes in order to improve efficiency and quality. LMS uses many lean tools to improve production and efficiency by getting the most out of each resource. However, Kaizen, 5S (now 7S), Kanban, Value Stream Mapping, 5Y’s, TPM, Visual Management, POKA YOKE (mistake proofing) PDCA etc. are among the most useful lean tools.
QSC can help you deliver a higher quality product to customers in a faster and more predictable way – a win for both your operations and your customers.

Value stream mapping
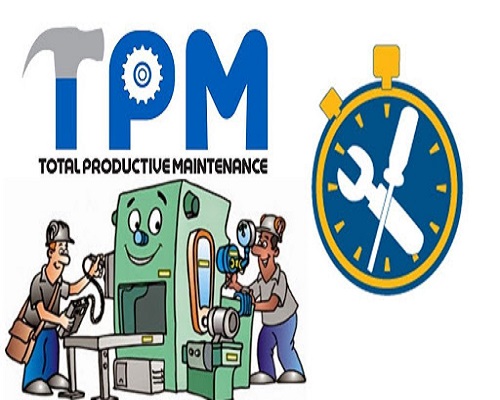
Total Productive Maintenance
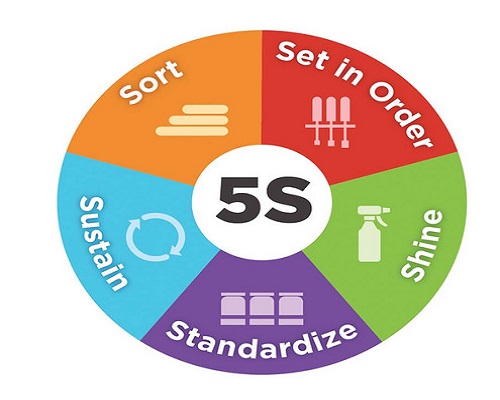
5S Methodology.
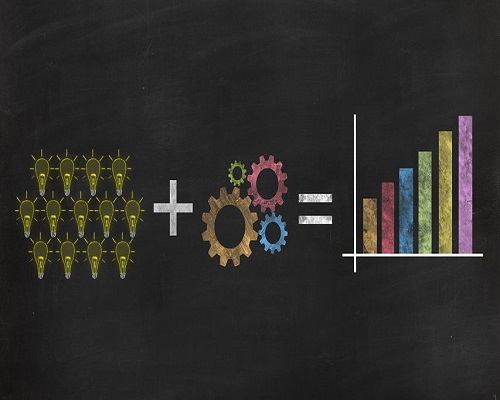
PDCA-Problem Solving
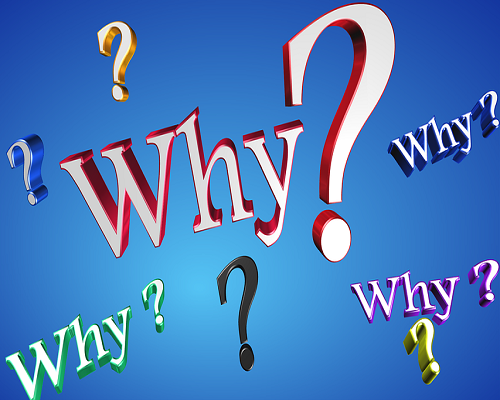
5 Whys
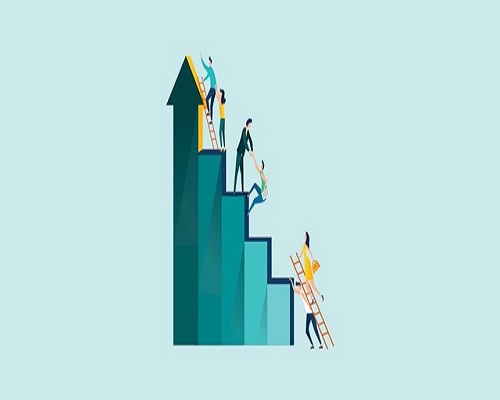
Root Cause Analysis
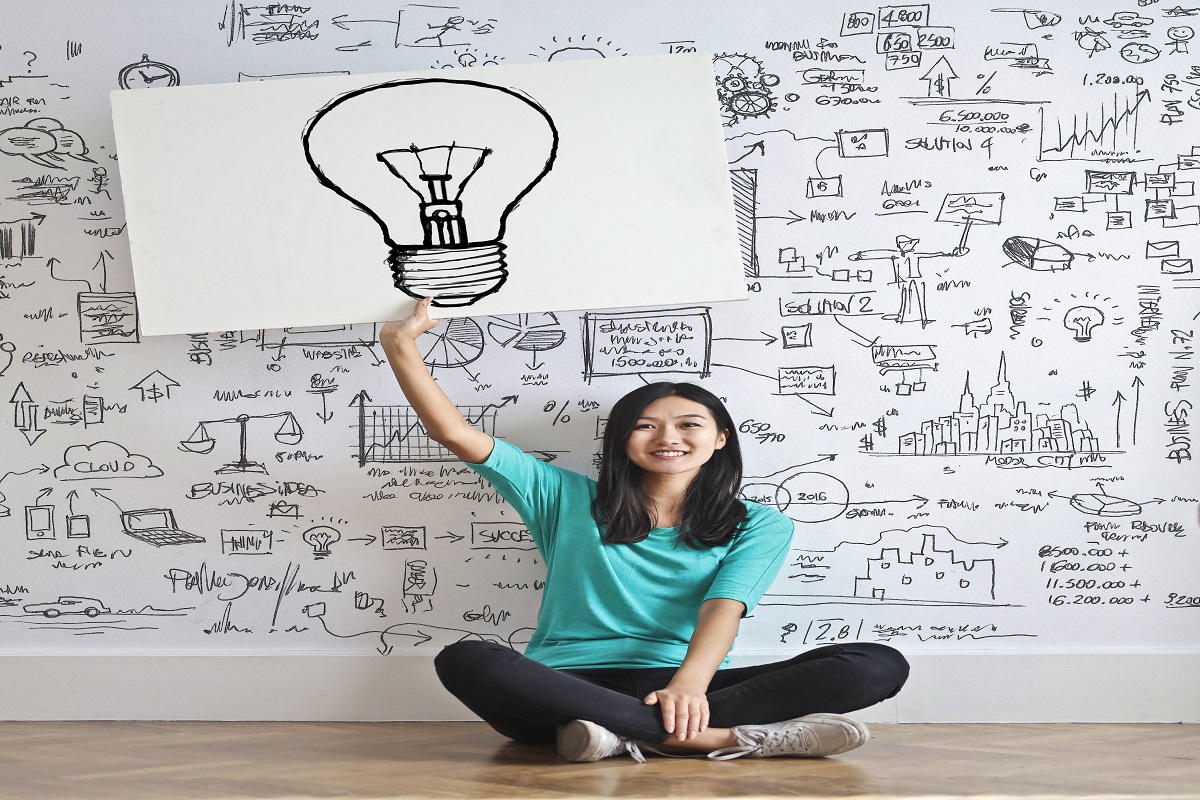
Six Sigma
Six Sigma is a disciplined, statistical-based, data-driven approach and continuous improvement methodology for eliminating defects in a product, process or service. Six Sigma can also be thought of as a measure of process performance, with Six Sigma being the goal, based on the defects per million. The name Six Sigma is derived from the bell curve used in statistics where one Sigma represents one standard deviation away from the mean. The defect rate is said to be extremely low when the process exhibits Six Sigma’s, where three are above the mean and three below. Six Sigma is simply a process for solving a problem. “DMAIC” as the 6S methodology is called consists of five basic phases:
- Define – Defining the problem, opportunity for improvement or any customer requirement
- Measure – Map and measuring the current process to gauge how it is performing,
- Analyze – Determine the root causes creating the problem and arrive at the solution,
- Improve – Improve the process by implementing and verifying the solutions, and
- Control – Control the improved process and maintain the solution
QSC certified Six Sigma Experts offers qualitative knowledge, guidance and direction in streamlining your business processes in producing and realizing the best products and services with the least number of defects.
Human resource management (HR) is a central pillar of all organizations. HR departments are responsible for
activities spanning a wide variety of core functions.
HR plays a key role in developing, reinforcing and changing the culture of an organisation.
Pay, compensation, legal compliance, performance management, training and development, recruitment and
onboarding, safety and health, employee and labor relations and reinforcing the values of the business are
all essential elements of business culture covered by HR.
Human resource is a discipline that requires leadership and management training necessary to build the
skills that business executives are looking for.
HR practitioners who have a deeper knowledge of relevant areas and more practical skills generate more
opportunities in the corporate world.
QSC provides various HR related services and helps boost fundamental soft skills of your
employees that enable building relationships and improve your productivity.
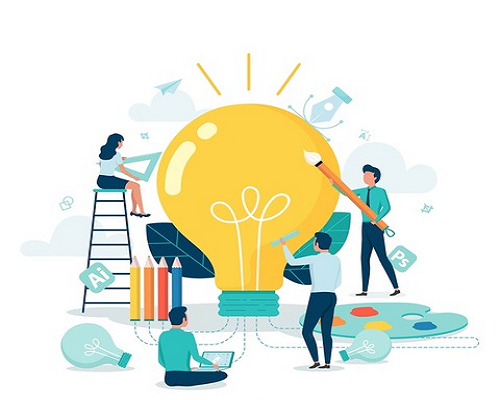
HR policies & processes
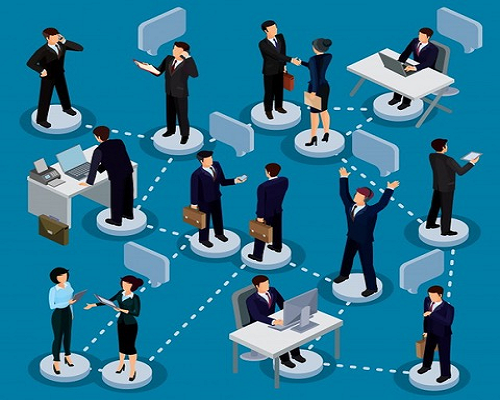
HR audits
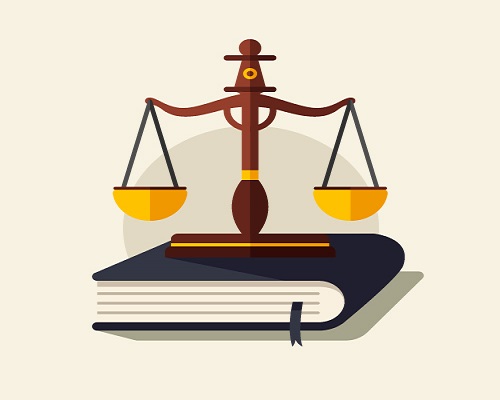
Legal compliance
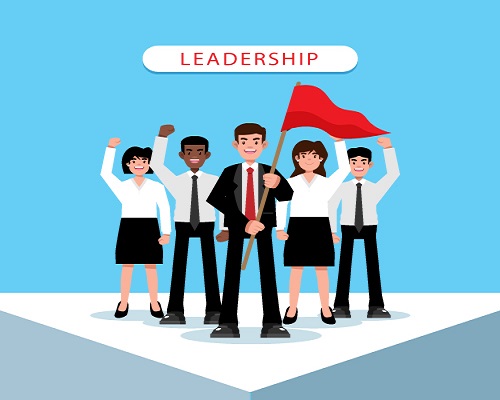
Leadership
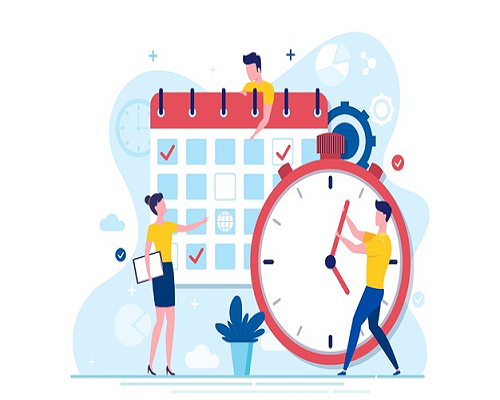
Time Management
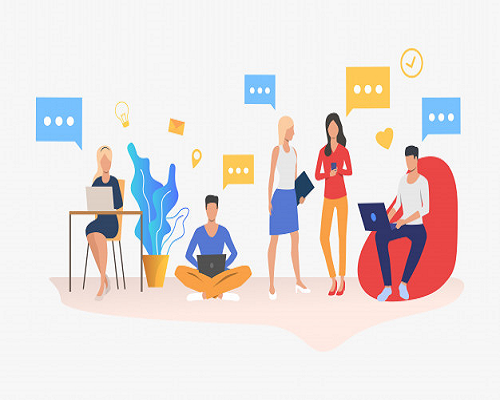
Communication skills
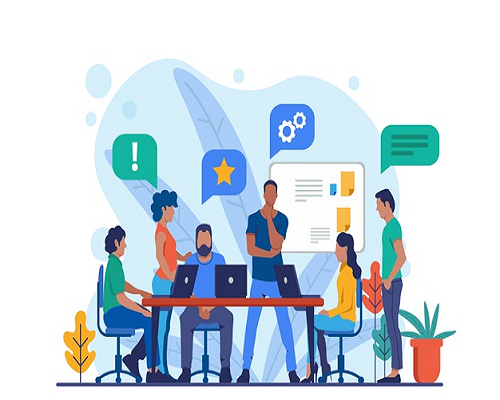
Teamwork
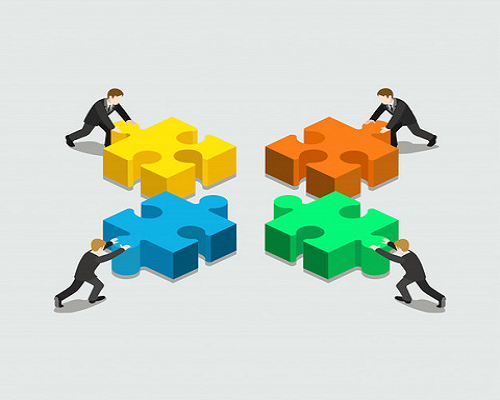
Problem Solving
Audits
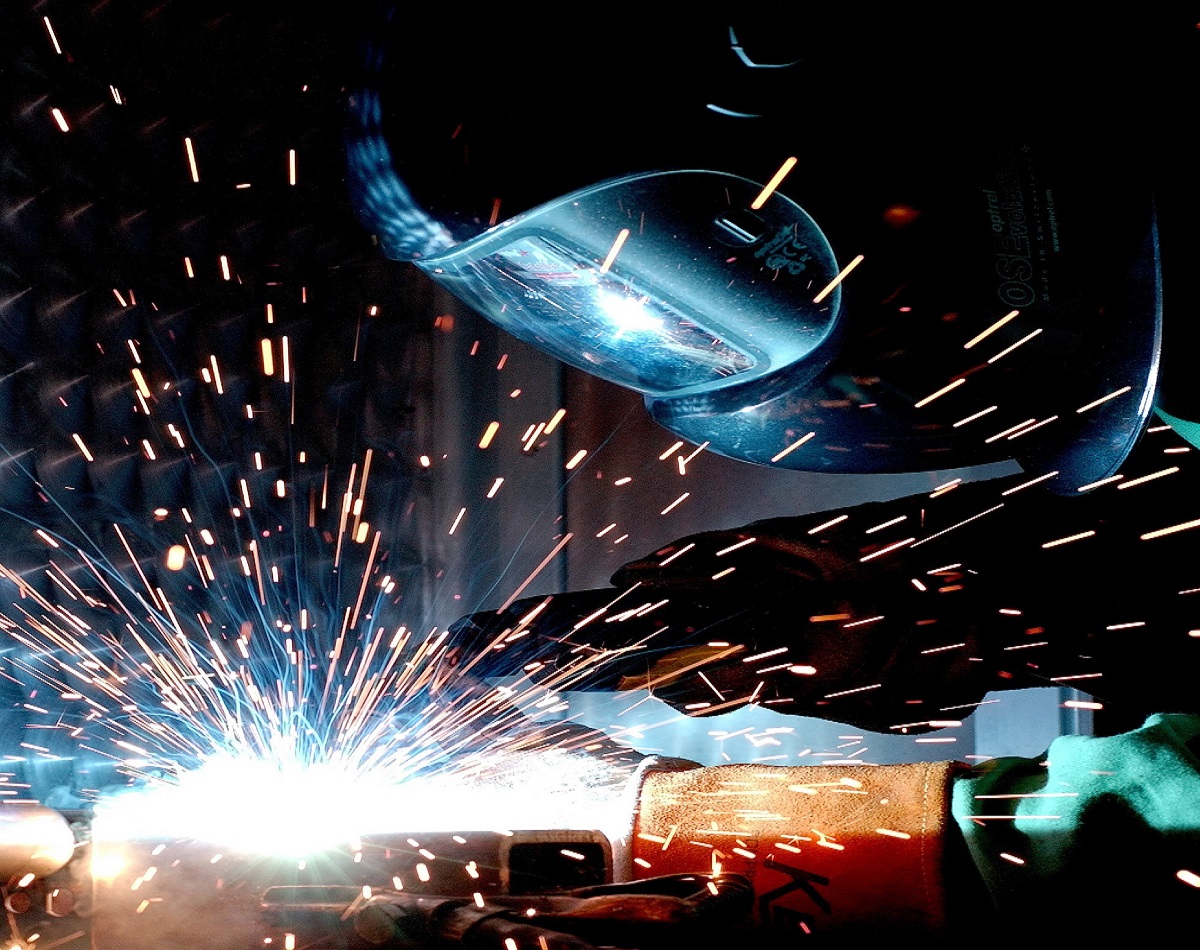
Special process Audits
A special process as per ISO 9000 is a process where its resulting output cannot be verified by subsequent monitoring or measurement. The ability to achieve planned results of such special processes needs to be validated and periodically revalidated. Automotive Industry Action Group (AIAG) has published a series of CQI standards (Continuous Quality Improvement) for the special processes which include:
- CQI 09 for Heat treatment
- CQI 11 for Plating
- CQI 12 for Coating
- CQI 15 for Welding
- CQI 17 for Soldering
- CQI 23 for Molding
- CQI 27 for Casting
QSC auditors are experts in your automotive industry and also certified to a range of automotive industry standards. Having worked with OEMs and throughout the automotive supply chain, our auditors can identify process cum operational issues and optimize process performances.

Supplier Audits
Supplier issues can cost organizations loads of money and most important result in customer rejections and dissatisfaction. As your business grows, so does the supplier base grow and so do the associated risks with each supplier. Every time you induct a new supplier you bring in risks of poor performance. Supplier audits are the most effective way to evaluate and select suppliers without letting in those risks and preventing the issues from turning into bigger problems. Supplier audits help you verify if the supplier’s quality systems, processes or products meet your requirements as defined in your contractual agreements and/or agreed standards.
Organizations mostly have difficulties in the covering the audits of the entire supplier base and often lack the technical process and product knowledge.
QSC can help you manage your supply chain efficiently by auditing your suppliers to identify potential risks, gauge compliance to your business requirements, uncover potential gaps in their quality and manufacturing processes and moreover align them with your business goals.
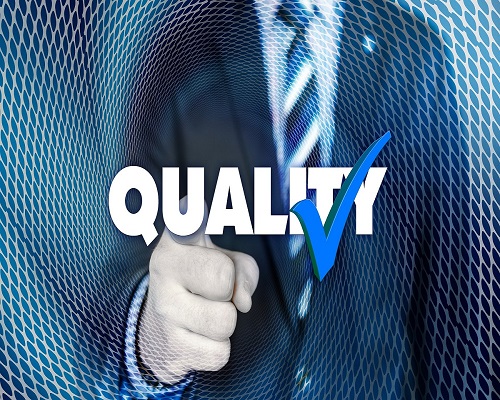
Process/Product Audits
Process audits help verify whether processes are performing well within specified controls and established limits. A process audit may check adherence to defined process parameters like time, temperature, speed, pressure, chemical composition, responsiveness, composition of any mix, service and transaction outcomes. It can further help to establish the adequacy, effectiveness and efficiency of the defined process specifications within the standard operation procedures, quality plans, test plans, control plans etc.
Product audit are an inspection of a final product / service before delivering it to a supplier or a customer. It often extends to assessing the packaging specifications and shipment requirements including transportation and preservation requirements. Product audit is an examination of a particular product or service, such as hardware, processed material, or software, to evaluate whether it conforms to requirements (i.e., specifications, engineering drawings, performance standards, and customer requirements. It is often referred to as a quality audit.
QSC’s process/product auditors have a varied and rich experience in almost all manufacturing processes, products and services. Being well versed with the technical requirements of the process and product including associated risks and customer requirements they can help accelerate your performance.
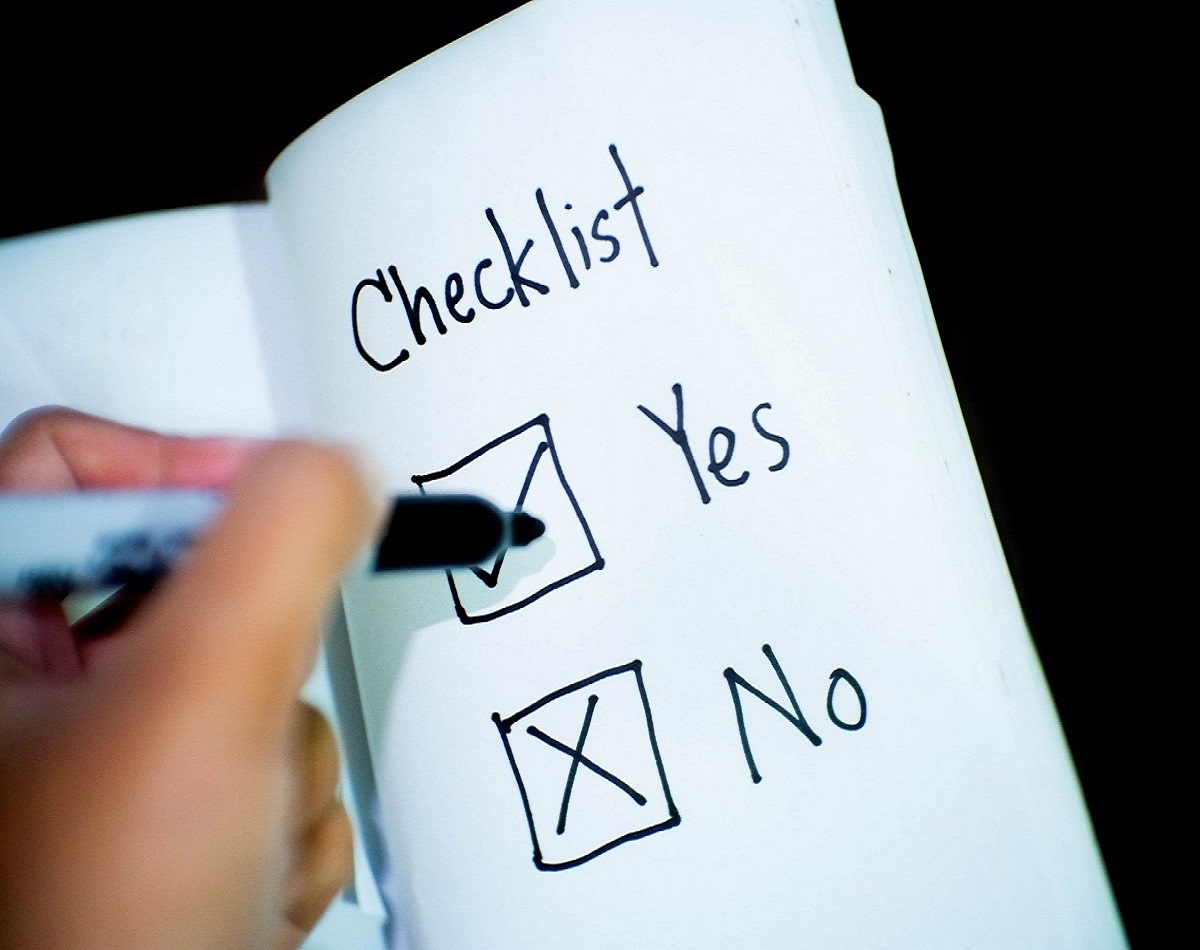
Internal Audit
An internal audit is a vital component to ensure optimal performance of your management systems, be it Quality, Environment, Health, Safety, Information Security, Aerospace, Automotive or any management systems. The role of an internal audit is also to provide independent assurance that an organisation’s risk management, governance and internal control processes are operating effectively. Internal audits can also assist in monitoring the defined system and checking applicable legal requirements are complied to including customer requirements. Typically, there are four phases in any internal audit – planning, conducting, reporting and follow up as required by ISO 19011.
QSC auditors are trained, qualified and certified in all the management systems including requirements of ISO 19011. We help you plan your audits, conduct value added audits using standard specific prescriptive audit checklists and provide a detailed report on the overall conformances, risks or weakness that exist in your processes, areas of improvement and non-conformances if any.
Training
QSC always strives to provide the best training courses including course materials and certifications that are specific to your industry and all levels of operations. Course materials are prepared and continually updated by highly experienced industry experts for professionals of all experience and skill levels. Courses are taught by industry experts having a rich industry and teaching experience that let organizations and individuals gain and apply the knowledge and skills acquired in our trainings.
QSC offers operational excellence courses that helps employees achieve self-sufficiency, cost savings, decreased repair and rework and increased ROI. Our management systems courses help organizations and process owners understand what the requirements of the management systems are, how to implement and establish the management system requirements, how to audit and continually improve the established management systems.
QSC with its extensive training experience can also work with your organization to provide Bespoke Training Courses. Our training experts understand your training needs, build and help deploy training solutions that bring tangible business benefits.
Call 9850576267 or write to us info@qualsiddh.com for your bespoke training needs.
QSC offers and conducts :
- Public courses
- On-site courses
- Virtual (On-line training)
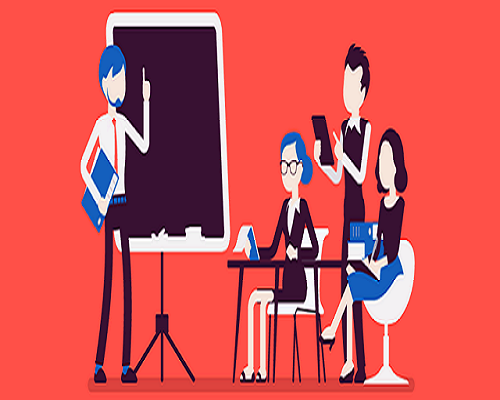
Operational Excellence Courses
- 7 QC tools
- 5S / 7S
- Kaizen
- Problem Solving Techniques
- Effective Root Cause Analysis
- APQP & Control Plan
- PPAP
- FMEA
- MSA
- SPC
- 8D Methodology
- AIAG CQI series
- Risk Management
- EMS Aspect Impact Identification
- OHS Hazard & Risk Assessment
- First Aid
- Fire-fighting
- ISMS Vulnerability Assessments
- ISMS Penetration Testing
- Implementing ISMS policies
& controls and many more…
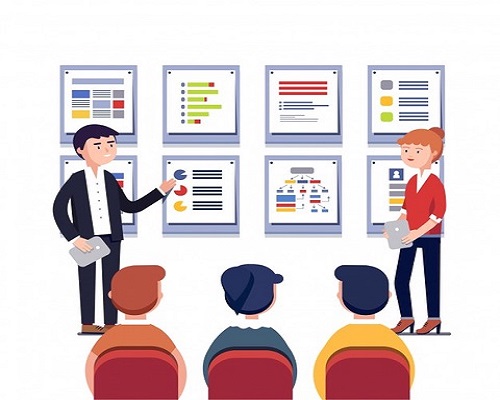
Management System Courses
- 1 Day – Awareness Course – For individuals who wish to gain basic knowledge of the relevant standard.
- 2 Day – Foundation Course – For individuals who wish to gain detailed knowledge of the relevant standard & its requirements
- 3 Day – Internal Auditor Courses – For individuals who wish to become internal auditors and audit their organizations processes.
- 5 Day – Lead Auditor Courses – For individuals who wish to conduct third party audits of the relevant standard & its requirements.
- 5 Day – Lead Practitioner Courses – For individuals who are responsible to establish, implement and manage the relevant standard in their organizations.
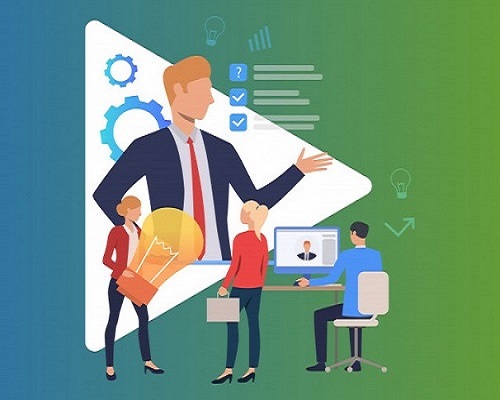
Virtual (on-line) Courses
Short of budget? Schedule Flexibility? Not much time to travel?
Try our Virtual Training courses. Our trainers although away from your workplace, create a conducive classroom atmosphere, increased participation and engagement with your other fellow learners and a great learning experience.
Call us on 9850576267
Email us at info@qualsiddh.com to know more about our virtual training courses.
Consultancy
QSC consultants have an average working experience of 25 years in manufacturing, service and IT sector. Our consultants understand your requirements, carry out an as-is mapping of your business processes,identify areas of improvement, facilitate process definitions, conduct counselling sessions in implementing processes and help businesses achieve excellence and customer satisfaction.
QSC also provides similar end-to-end consultancy services to help its customers achieve third party certifications to various ISO management system standards or continual improvement in your existing business practices.
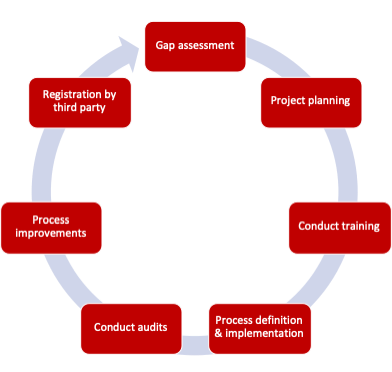
Quality Management System
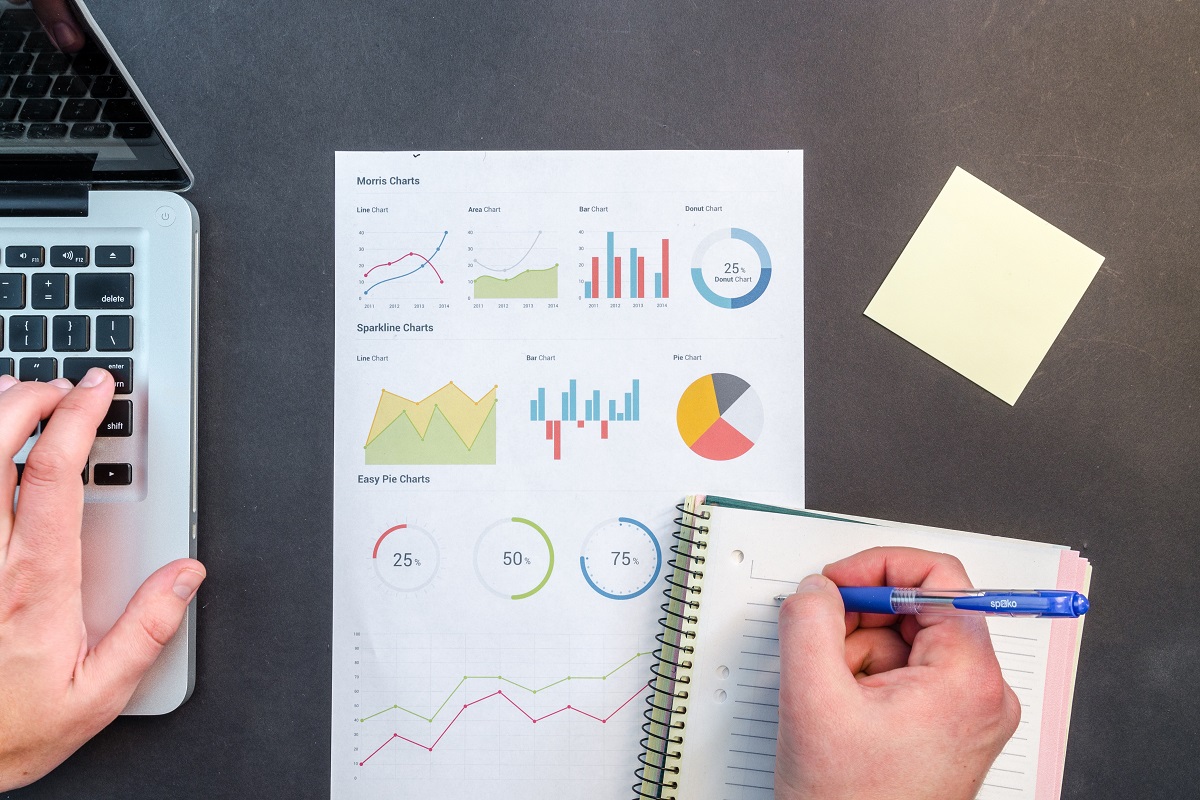
ISO 9001
ISO 9001 is defined as the international standard that specifies requirements for a quality management system (QMS).
Organizations use the standard to demonstrate the ability to consistently provide products and services that meet customer and regulatory requirements.
Being ISO 9001 certified is well worth the effort and time put into it.
Not only will your organization be more efficient and quality-driven, but your employees and customers will also see a significant, positive difference!
QSC helps its customers establish a quality management system (QMS) ensuring that the entire organization works together towards the continuous improvement of the processes, products, workflows, and culture to meet customer expectations, it’s applicable legal requirements and attain business goals in a streamlined manner.
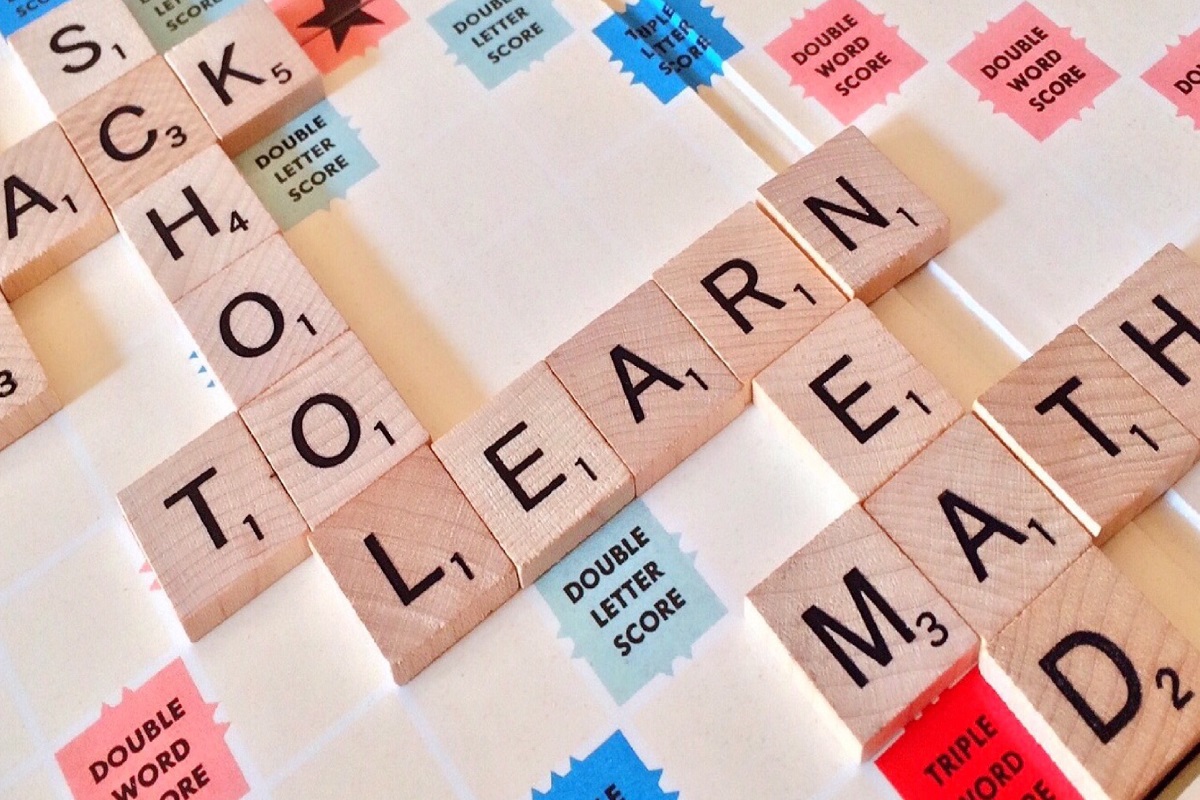
ISO 21001
The new ISO management system standard for educational organizations (EOMS).
ISO 21001 is the newly published standard recently in 2018 and is now the preferred standard for educational institutes / organizations. Educational organizations include pre-school, primary, elementary, middle schools, high schools, colleges, universities, adult education, vocational education and training, tutoring or coaching centers, training organizations.
ISO 21001 – EOMS is intended to provide a common management tool for organizations providing educational products and services capable of meeting learner and other customer requirements and needs.
QSC till date has helped many business management, catering and technical institutes in establishing and educational management systems and getting them certified by an accredited third-party registrar.
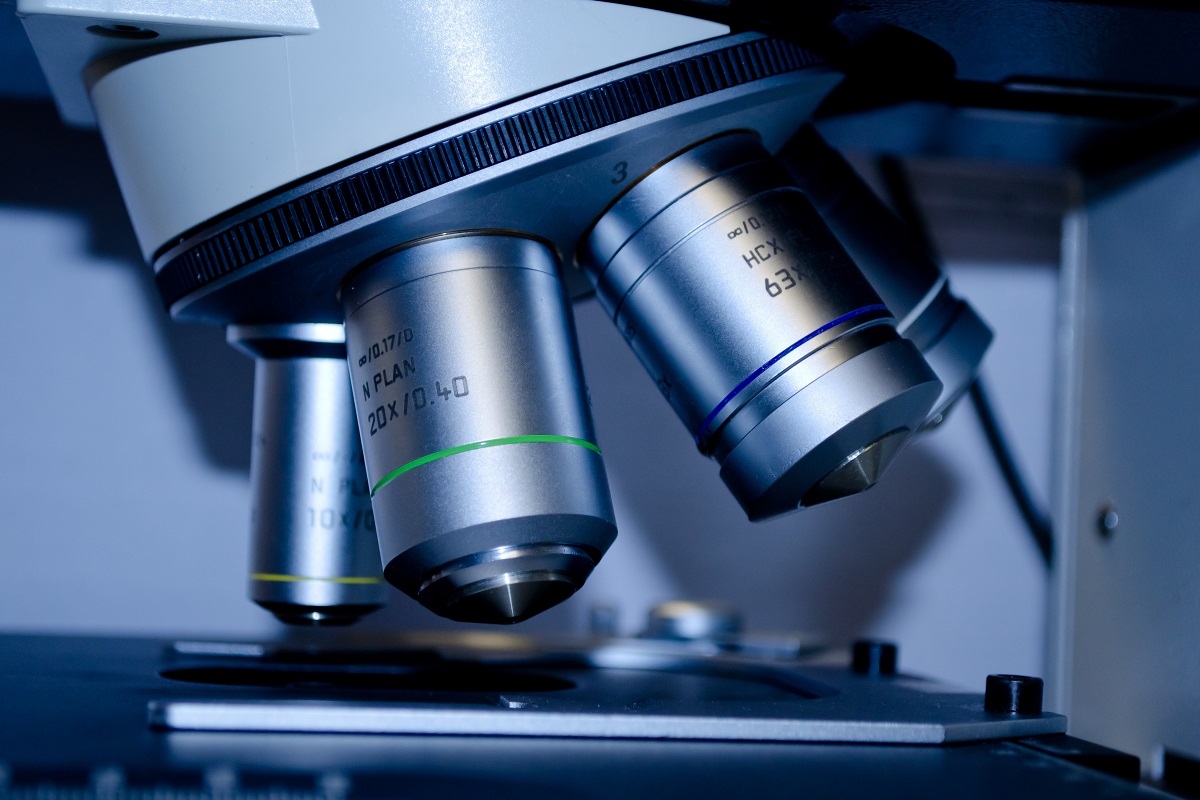
ISO 13485
This internationally agreed standard sets out the requirements for a quality management system specific to the medical devices industry.
A medical device is a product, such as an instrument, machine, implant or in vitro reagent, that is intended for use in the diagnosis, prevention and treatment of diseases or other medical conditions.
ISO 13485 is designed to be used by organizations involved in the design, production, installation and servicing of medical devices and related services.
ISO 13485 firmly ensures the use of best practices throughout all steps of a medical device’s life cycle.
Most importantly serves as a regulatory & legal requirement in many countries.
QSC experts will offer you a qualitative experience ensuring your requirements are met.
Sustainability Management System
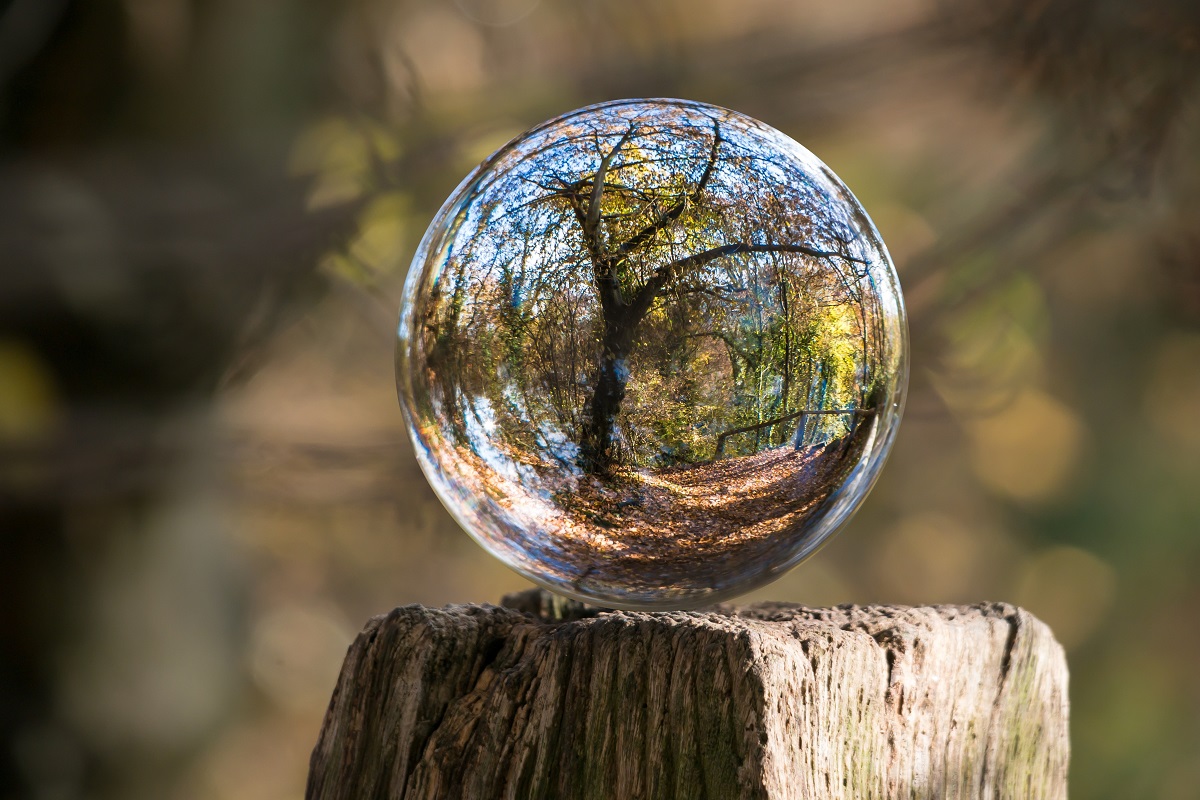
ISO 14001
ISO 14001 is the most widely used Environmental Management System (EMS) standard in the world that helps you to control your environmental aspects, reduce impacts and ensure legal compliance.
Designed for any type of organization, regardless of its activity or sector, it can provide assurance to company management and employees as well as external stakeholders that environmental impact is being measured and improved.
Issues including air pollution, land and groundwater contamination, disposal of hazardous wastes and E-waste are the main concerns of governments, industries and customers.
QSC’s environmental experts help you to establish and implement an EMS which not only improves your environmental performance but grow your business in a sustainable manner.
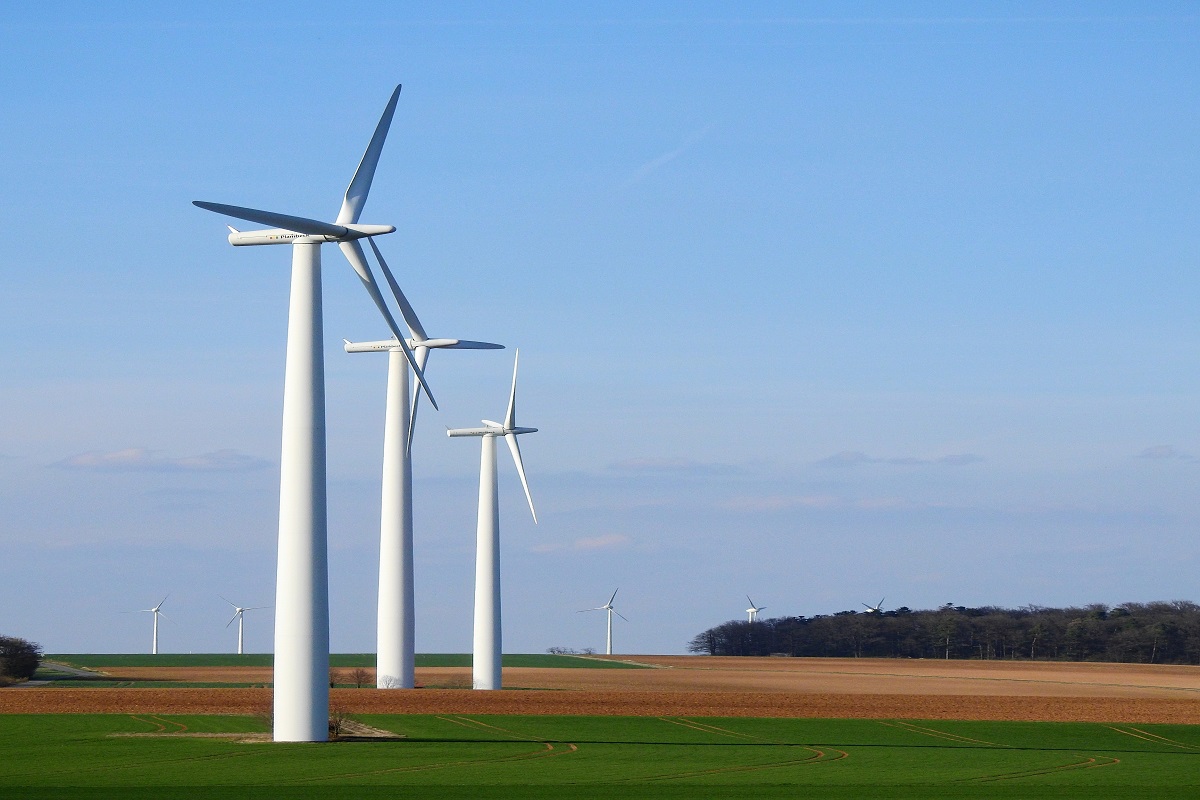
ISO 50001
ISO 50001 specifies Energy Management Systems (EnMS) requirements for any organization looking at reducing energy consumption and improving energy efficiency.
It enables organizations to establish the systems and processes necessary to continually improve energy performance, energy use and energy consumption.
Energy often is the highest operating cost for any organization.
By improving energy performance and associated energy costs, organizations can be more competitive.
In addition, implementation can lead organizations to meet overall climate change mitigation goals by reducing their energy-related greenhouse gas emissions.
QSC helps organizations to realize untapped energy efficiency potential.
Health & Safety Management System
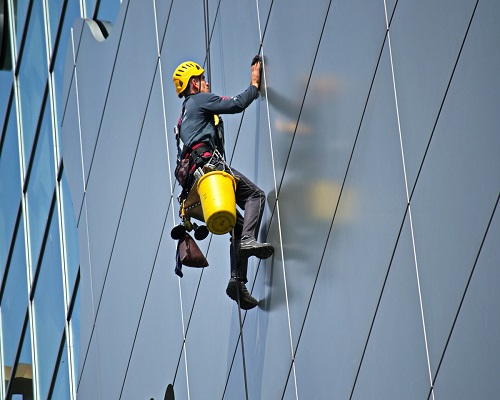
ISO 45001
ISO 45001 is the newly developed international standard for Occupational Health & Safety (OHS) Management System and replaces OHSAS 18001.
Globally across all industries there are nearly 7500 plus incidents/accidents or diseases per day which is one of the prime reasons why health and safety is the number one priority of all businesses.Irrespective of the type of business / industry you are in, accidents that lead to injury or health related issues are always likely to occur.
Just like all other ISO standards, ISO 45001 too is applicable to all organizations, regardless of size, industry or nature of business.It requires that organizations integrate the OHS requirements into their existing business processes in order that organizations can increase their OHS performance.
Our safety experts enable organizations bring in place an OHS management system that helps manage OH&S hazards & risks and reduce workplace incidents leading to a healthy & safe work culture.
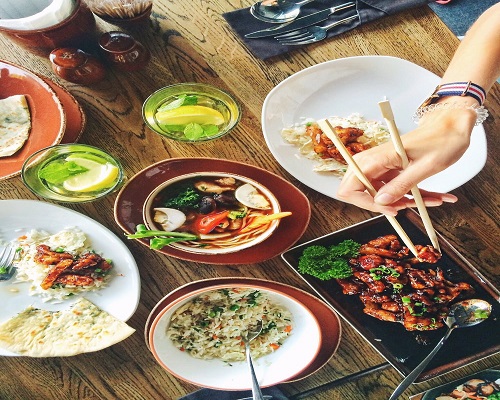
ISO 22000
A foodborne illness is a disease transmitted by food to people. Every year lakhs of people fall sick from unsafe food. A food safety management system can prevent these kinds of outbreaks and save a company thousands of rupees. ISO 22000 also referred to as Food Safety Management Systems (FSMS) is a sector specific standard that describes a specific process to direct and control food safety aspects. It helps the food business operators to gain this trust of the consumers or even serve them efficiently. ISO 22000 can also ensure regulatory compliance to ISO standards by actively controlling risks and hazards throughout the food process. Once identified, these hazards can be prevented, eliminated, or reduced to safe levels.
QSC can help your company implement an effective FSMS keeping both your business and the public safe from foodborne illnesses.
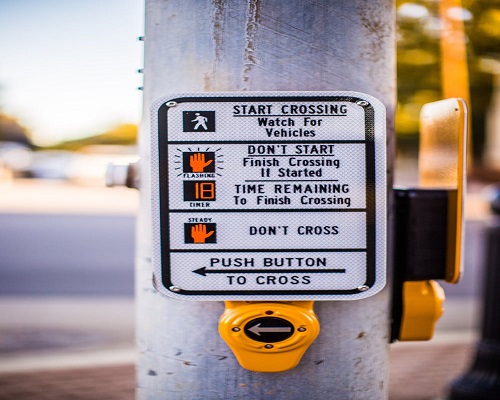
ISO 39001
ISO 39001 – Road Traffic Management Systems (RTSMS) specifies requirements for any organization, public and private, that interacts with road safety systems. Every minute someone is killed in a road accident and claims a life of a near and dear one within a family.The ultimate goal of the RTSMS is to eliminate road fatalities and serious injuries associated with road traffic accidents.
Implementing ISO 39001 helps contribute to the national and global efforts to prevent fatalities and injuries in road crashes and demonstrate organizations commitment to issues that can be of public concern.
QSC can help organizations set up road traffic processes needed for safer mobility, identify RTS performance factors and improve RTS performance.
Aerospace Management System
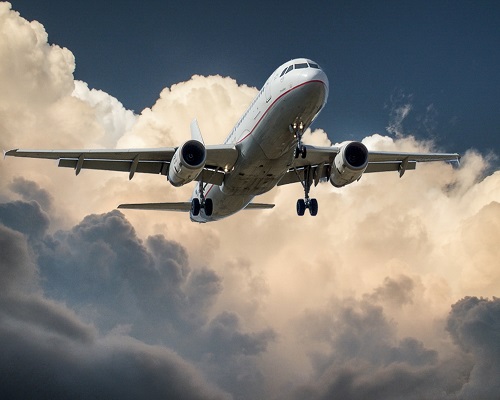
AS9100
AS9100 is the international Quality Management System standard for the Aviation, Space and Defense (AS&D) industry, created by the International Aerospace Quality Group (IAQG). AS9100 was established with the primary aim of providing safe and reliable products for the aerospace industry.
It is used and supported by the world’s leading aerospace companies and throughout their supply chains.
This standard is intended for use by organizations that design, develop, or provide aviation, space, and defense products and services.The Aviation Industry is highly regulated with demands and controls that ensure the safety and reliability of equipment and materials.
The industry relies heavily on suppliers demonstrating effective management systems.
AS 9100 sets the quality levels expected in all areas of aerospace, from commercial to defense aviation.
QSC helps organizations develop Aerospace QMS ensuring your internal processes improve and achieve customer expectations.
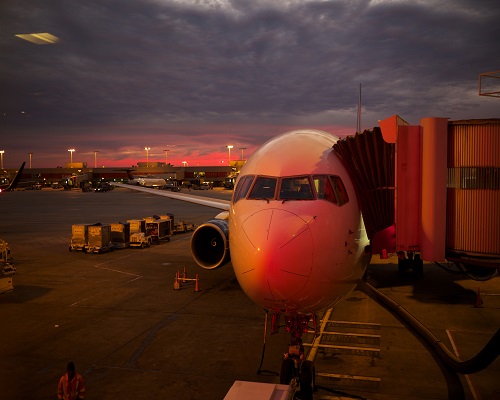
AS9110
AS9110 is a standard intended for use by organizations whose primary business is providing maintenance or continuing airworthiness management services for civil or military aviation articles and products and by original equipment manufacturers with maintenance, repair, and overhaul operations that are operated autonomously, or that are substantially different from their production operations.A standard supported by International Aerospace Quality Group (IAQG) is based on AS9100 and adds specific requirements that are critical for the Maintenance, Repair & Overhaul (MRO) of commercial, private, and military aircrafts.
QSC helps organizations develop management systems which meet these requirements and achieve registration to AS9110.
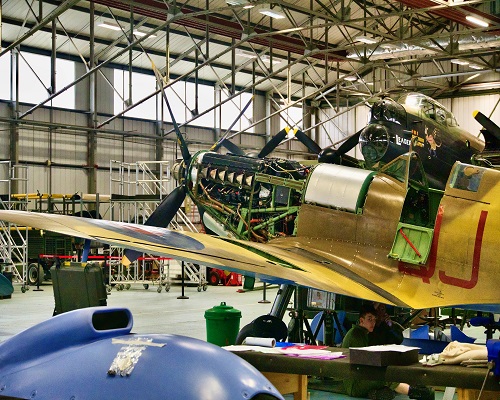
AS9120
AS9120 – Quality Management Systems – Aerospace Requirements for Stockist Distributors – was developed for stockist or pass-through distributors of aerospace commodity items.
Society of Automotive Engineers (SAE) manages this standard which is regulated by the IAQG (International Aerospace Quality Group).This standard is part of the AS9100 series and addresses chain of custody, traceability, control and availability of records of companies that procure parts, materials and assemblies and sells these products to a customer in the aviation, space and defense industries.
This includes organizations that procure products and split them into smaller quantities.
The standard would be applicable for organizations that resell, distribute, and warehouse parts found in aircraft and other aerospace components.
QSC works towards aligning your operations to meet these requirements for inventory control, lot tracing, and vendor management, ensuring consistency throughout their supply chain.
Automotive Management System

IATF 16949
IATF 16949 developed by the International Automotive Task Force (IATF) with support from Automotive Industry Action Group (AIAG), is a global Quality Management System Standard for the Automotive industry.IATF 16949:2016 incorporates the structure and requirements of the ISO 9001:2015 quality management system standard with additional automotive customer-specific requirements. The standard applies to all manufacturers in the automotive supply chain worldwide – for cars, their parts, components or systems. Certification to this technical specification provides global recognition for suppliers sourcing across the automotive industry.
Some of the vital key focus areas of IATF 16949 includes continual improvement, defect prevention, reducing waste, product safety & above all risk management.
QSC has experienced automotive industry experts who will help you make continuous improvements to your systems and process quality and place customer-specific requirements at the heart of what you do.
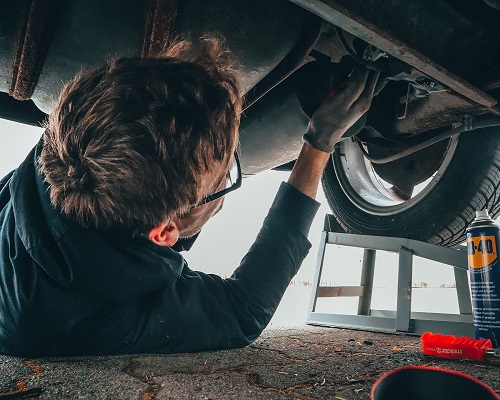
VDA 6.3
VDA is the German abbreviation for the “Association of the Automotive Industry” (Verband der Automobilindustrie e.V.). Developed by VDA QMC and the German automotive industry, VDA 6.3 defines a process based audit standard for evaluating and improving controls in a manufacturing organization’s processes. This association publishes guidelines for the automotive industry for the implementation of standards and the realization of OEM requirements. The standard can be used by any organization, either for internal process audits, or for evaluating potential or existing suppliers. The standard can also be used by any organization, either for internal process audits, or for evaluating potential or existing suppliers. Compliance to VDA 6.3 is mandated by some vehicle makers and encouraged by others.
QSC experts are qualified and certified by VDA-QMC and can help deploy these German automotive requirements.
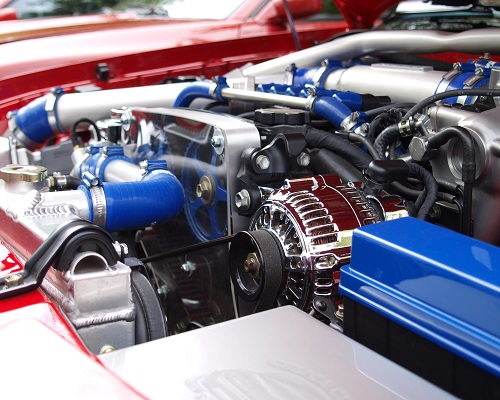
A- SPICE
A-SPICE stands for Automotive Software Process Improvement and Capability dEtermination. It is yet another standard developed by the German Automotive Industry. Automotive projects are getting more complex by the day and the focus has changed from mechanical challenges to more software’s in the car.Expectations of the customer in terms of comfort, infotainment and safety are also increasing requiring automobile manufacturers to change their development process and moreover shorten the life cycle of their software projects. A-SPICE is an internationally accepted process model that defines best practices for software and embedded systems development for the automotive industry.
QSC consultants are qualified to conduct software life cycle audits and with the automotive manufacturing background are competent to help clients establish a process maturity framework thereby improving the automotive software development processes.
Information Security Management System
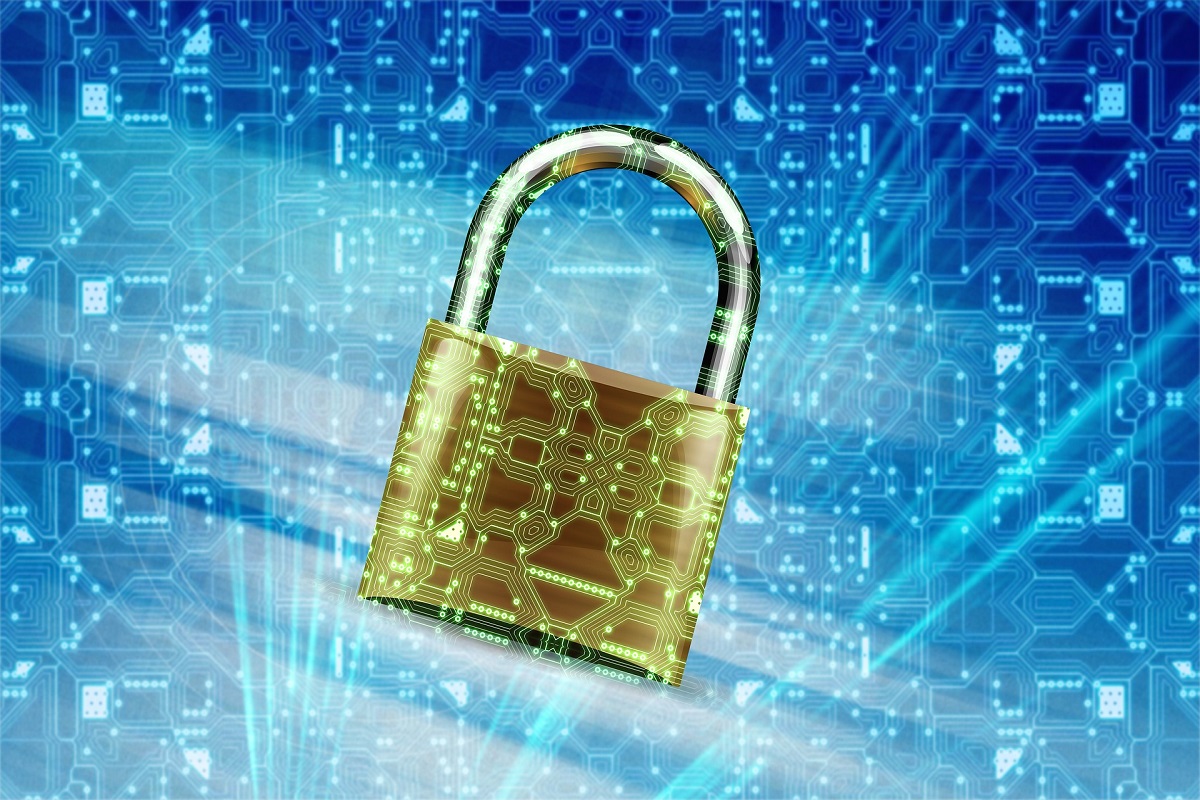
ISO 27001
Keeping information assets secure, be it financial, intellectual, employee related or managed by third parties, it has become crucial to all organizations and ISO 27001 is the most widely used and preferred standard that sets out the requirements for an Information Security Management Systems (ISMS).The standard covers all types of organizations from micro-businesses to huge multinationals, and all sectors like retail, banking, defense, healthcare, education and government. ISO 27001 works on three security goals Confidentiality, Integrity & Availability. ISO 27001 draws coordination between all sections of an organization and a framework of policies and procedures that includes all legal, physical and technical controls involved in an organization’s information risk management processes.
QSC experts assess the information risks that exist in your organization, identify applicable controls and help evolve an ISMS that continually improves the safety of your information.
Software Management Systems

CMMI
CMMI – Capability Maturity Model Integration as it stands for was developed by the Software Engineering Institute at Carnegie Mellon University as a process improvement tool for projects, divisions or organizations. The DoD and U.S. Government helped develop the CMMI, which is a common requirement for DoD and U.S. Government software development contracts. The CMMI is currently administered by the CMMI Institute, which was purchased by the ISACA in 2016.The Capability Maturity Model Integration (CMMI) helps organizations streamline process improvement, encouraging a productive, efficient culture that decreases risks in software, product and service development. CMMI defines the following maturity levels for processes: Initial, Managed, Defined, Quantitatively Managed, and Optimizing.
QSC’s CMMI consultants can help you successfully upgrade to the new CMMI 2.0 model or to a new implementation.
Service Management Systems
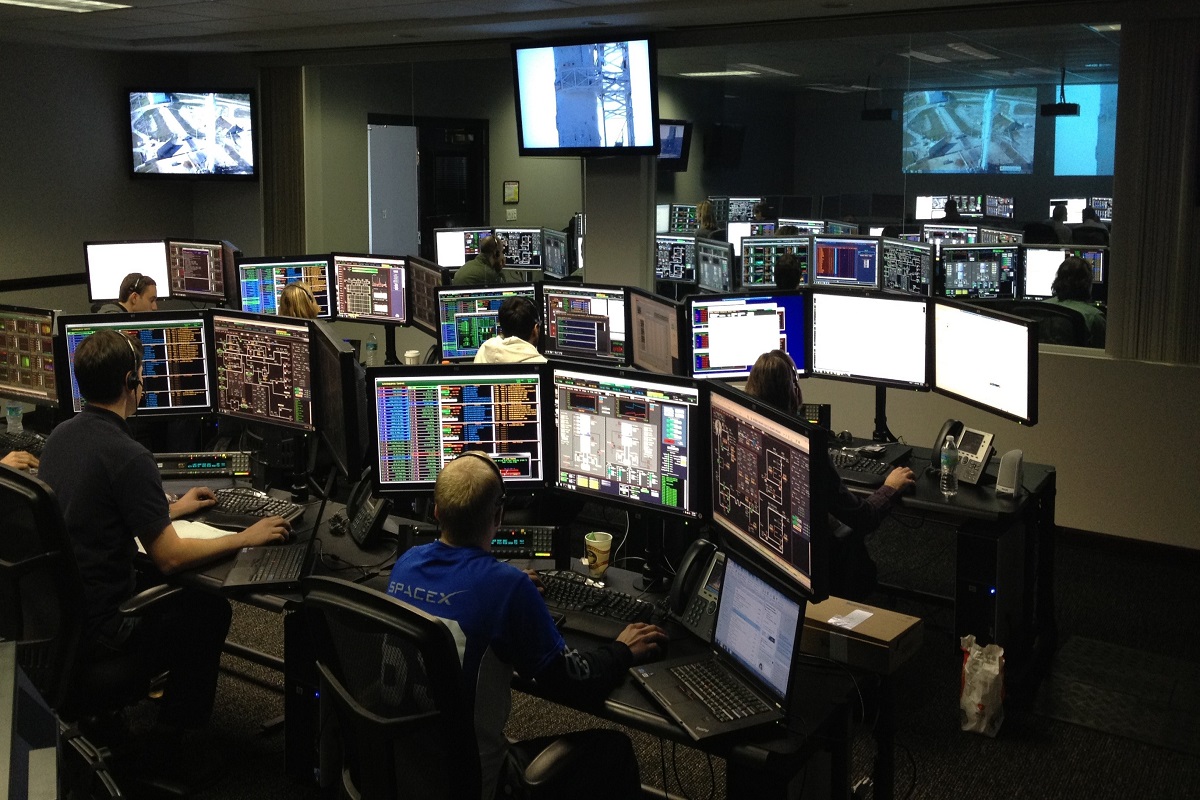
ISO 20000
ISO/IEC 20000 is the first internationally acknowledged standard for service management. It was developed in 2005 based on the earlier BS 15000, and subsequently revised in 2011 and 2018.
This standard specifies requirements for an organization to establish, implement, maintain and continually improve a service management system (SMS). The requirements specified include the planning, design, transition, delivery and improvement of services to meet the service requirements and deliver value.ISO 20000 certification confirms that an organization is conscious about their customers service deliverables, committed to service quality, has implemented number of IT controls that ensures fulfilment of IT Service Level Agreements, and IT availability risks.
QSC builds your skills and helps your organization become a competitive differentiator for the delivery of services.
Business Continuity Management System
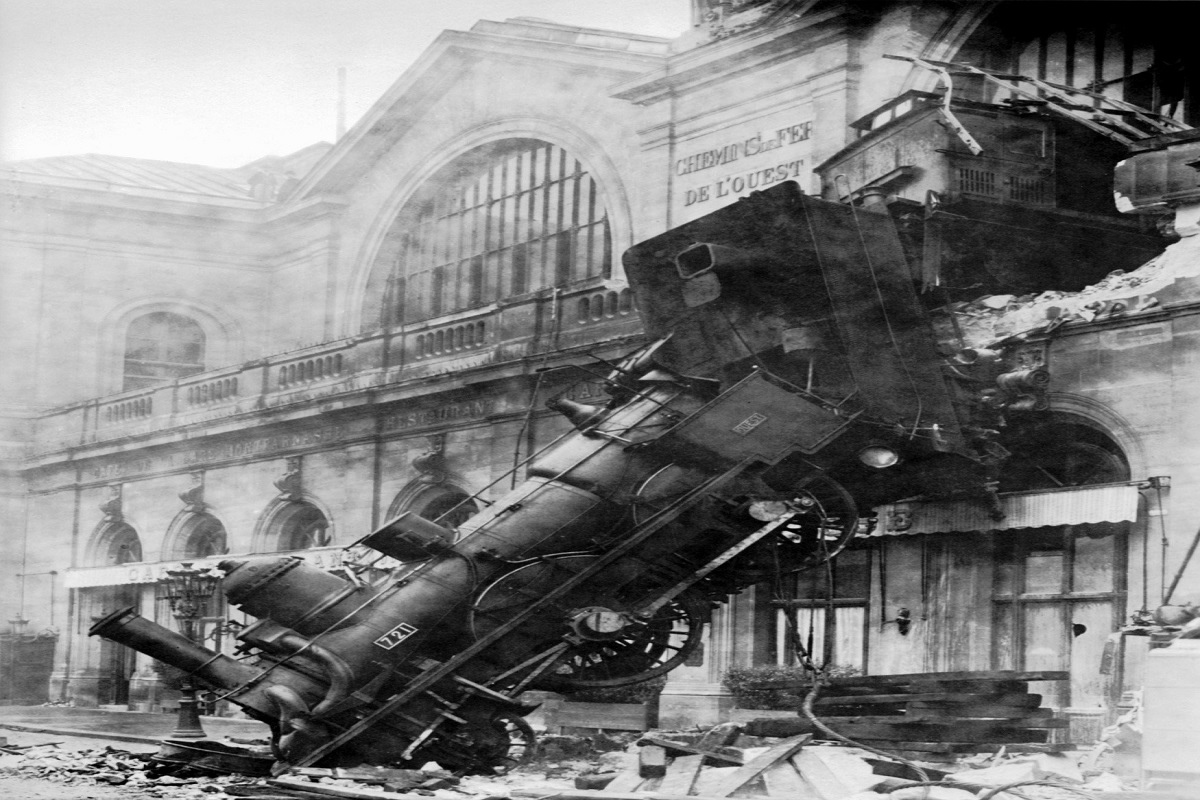
ISO 22301
ISO 22301 provides a framework to plan, establish, implement, operate, monitor, review, maintain and continually improve a business continuity management system (BCMS). It is expected to help organizations protect against, prepare for, respond to, and recover when disruptive incidents arise. Implementing a BCMS within your organization means that you are prepared for the unexpected. It helps you to manage risks to handle the threat of business activities or processes being interrupted by external and/or internal factors.Winning new business contracts, protecting revenue and profits, optimal recovery from a damaging incident, and compliance with regulatory requirements are all benefits of an ISO 22301-aligned BCMS.
QSC can help assessing your current business continuity arrangements against the Standard and provide you with a roadmap to implement an effective BCMS.
Supplier Development
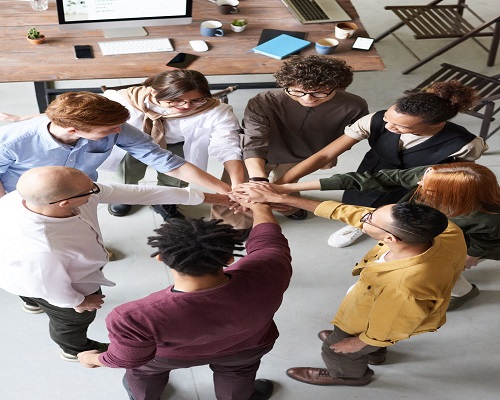
Supplier Development
Suppliers have a pivotal role at every stage of the product lifecycle. The role of a supplier in a business is to provide high-quality products. From sourcing raw materials to helping ramp up production, and to finding better options for raw materials as the market starts becoming saturated, companies need to work closely with their suppliers to get the best out of their products. Supplier development programs need to be a major focus of organizations who manufacture products and have a supply base because they lead to better overall relationships with suppliers and will improve communication, quality, and delivery as a result. Developing suppliers of vital goods and services can result in lower cost, improved quality and consistent on-time delivery.
QSC works with your identified suppliers on a one-to-one basis to improve their performance and ability to deliver goods or services that will satisfy your customers’ needs. Be it implementing any ISO management systems or PPAP implementation and submissions, following your own corporate policies, your Supplier Management Systems or conducting supplier audits to ensure your legal and process/product/customer requirements are met at all times, our consultants work collaboratively with your suppliers to boost their performance.
Lean Management Systems
“Simply put, Lean Management Systems (LMS) means creating more value for customers with fewer resources.” Used originally by manufacturing organizations, LMS is a performance-based, continuous-improvement strategy that focuses on eliminating waste and unnecessary steps in company processes in order to improve efficiency and quality. LMS uses many lean tools to improve production and efficiency by getting the most out of each resource. However, Kaizen, 5S (now 7S), Kanban, Value Stream Mapping, 5Y’s, TPM, Visual Management, POKA YOKE (mistake proofing) PDCA etc. are among the most useful lean tools.
QSC can help you deliver a higher quality product to customers in a faster and more predictable way – a win for both your operations and your customers.

Value stream mapping
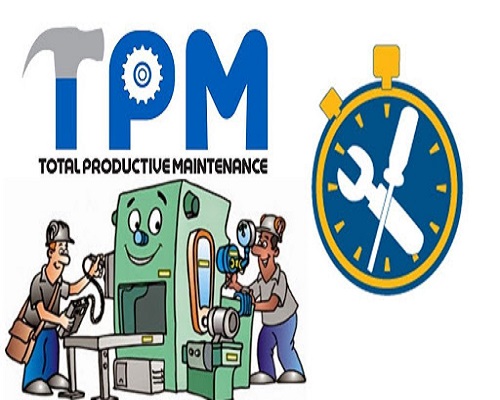
Total Productive Maintenance
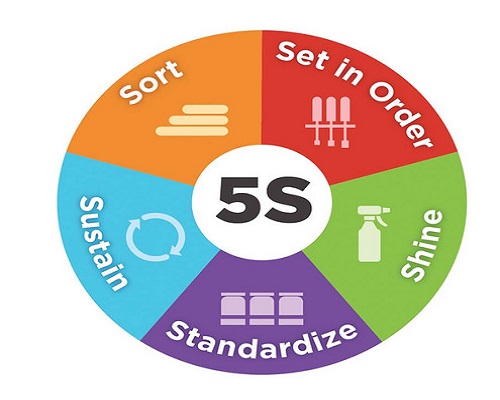
5S Methodology.
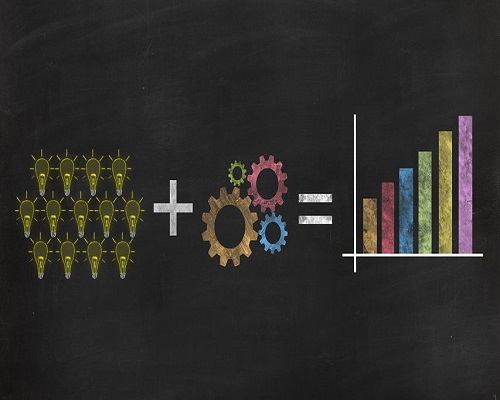
PDCA-Problem Solving
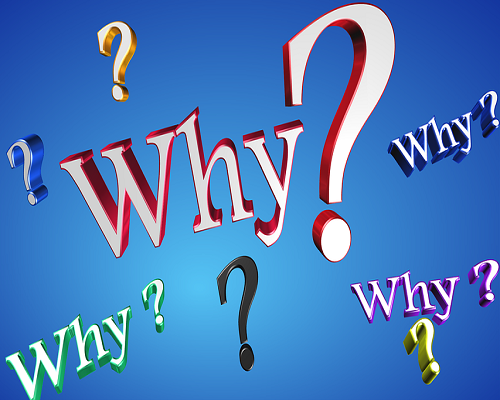
5 Whys
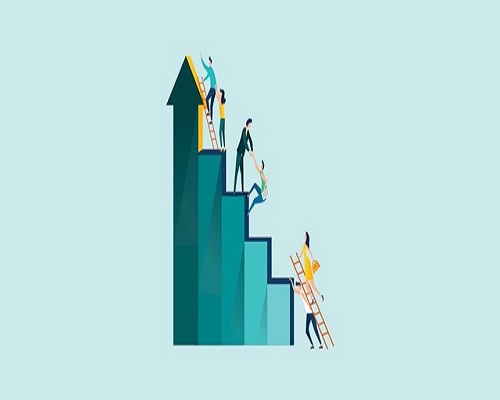
Root Cause Analysis
Six Sigma Methodology
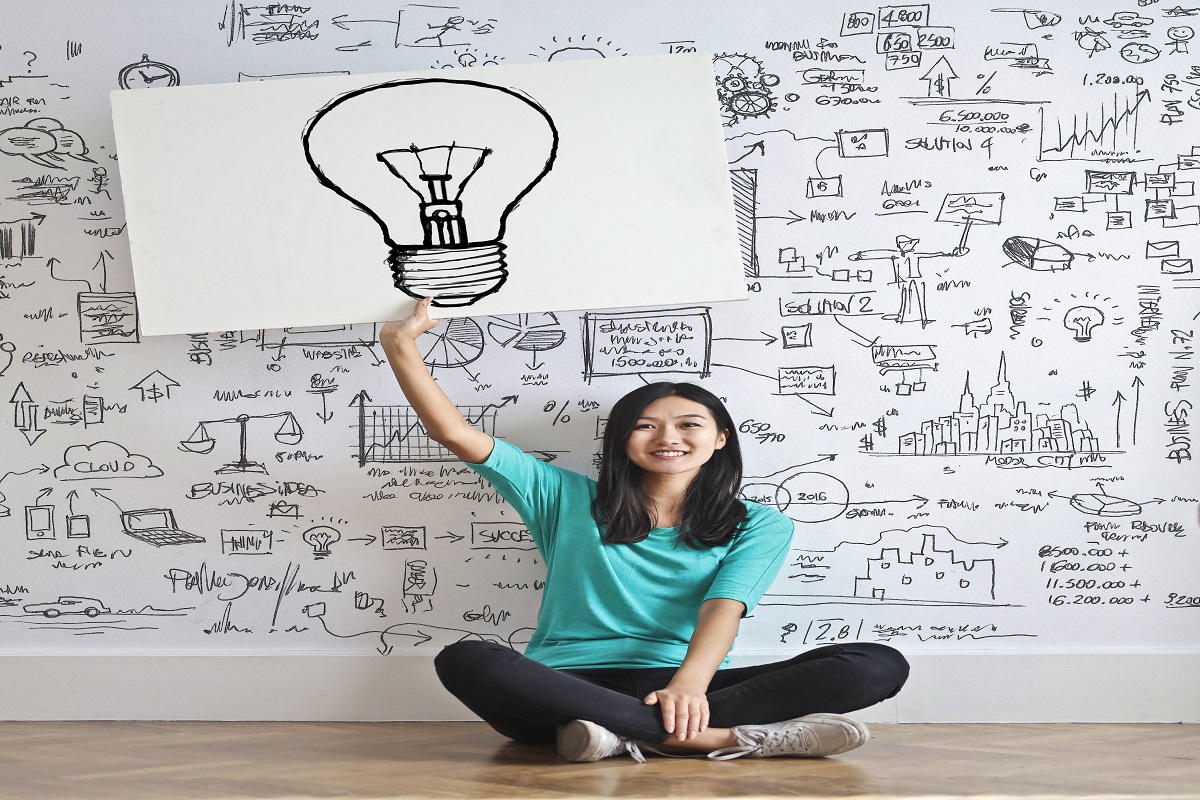
Six Sigma
Six Sigma is a disciplined, statistical-based, data-driven approach and continuous improvement methodology for eliminating defects in a product, process or service. Six Sigma can also be thought of as a measure of process performance, with Six Sigma being the goal, based on the defects per million. The name Six Sigma is derived from the bell curve used in statistics where one Sigma represents one standard deviation away from the mean. The defect rate is said to be extremely low when the process exhibits Six Sigma’s, where three are above the mean and three below. Six Sigma is simply a process for solving a problem. “DMAIC” as the 6S methodology is called consists of five basic phases:
- Define – Defining the problem, opportunity for improvement or any customer requirement
- Measure – Map and measuring the current process to gauge how it is performing,
- Analyze – Determine the root causes creating the problem and arrive at the solution,
- Improve – Improve the process by implementing and verifying the solutions, and
- Control – Control the improved process and maintain the solution
QSC certified Six Sigma Experts offers qualitative knowledge, guidance and direction in streamlining your business processes in producing and realizing the best products and services with the least number of defects.
HR & Soft Skills
Human resource management (HR) is a central pillar of all organizations. HR departments are responsible for
activities spanning a wide variety of core functions.
HR plays a key role in developing, reinforcing and changing the culture of an organisation.
Pay, compensation, legal compliance, performance management, training and development, recruitment and
onboarding, safety and health, employee and labor relations and reinforcing the values of the business are
all essential elements of business culture covered by HR.
Human resource is a discipline that requires leadership and management training necessary to build the
skills that business executives are looking for.
HR practitioners who have a deeper knowledge of relevant areas and more practical skills generate more
opportunities in the corporate world.
QSC provides various HR related services and helps boost fundamental soft skills of your
employees that enable building relationships and improve your productivity.
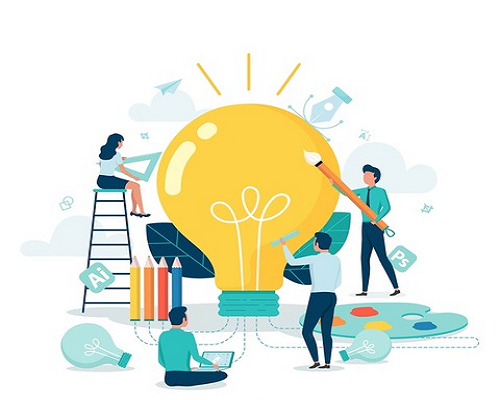
HR policies & processes
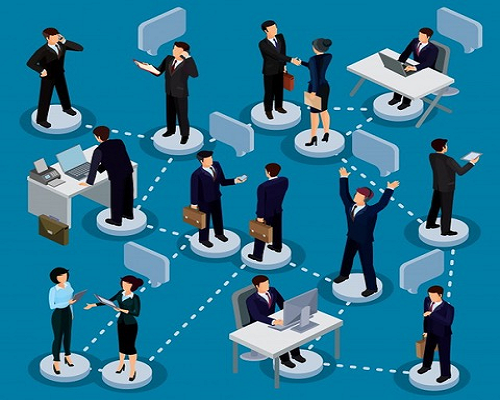
HR audits
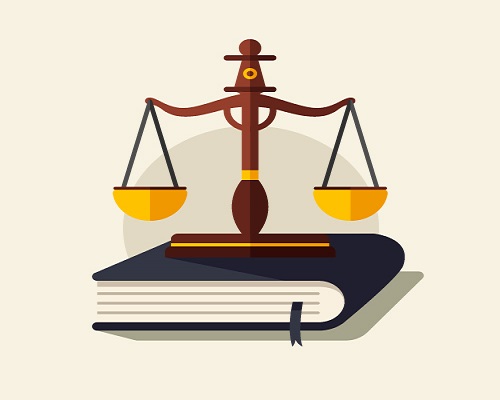
Legal compliance
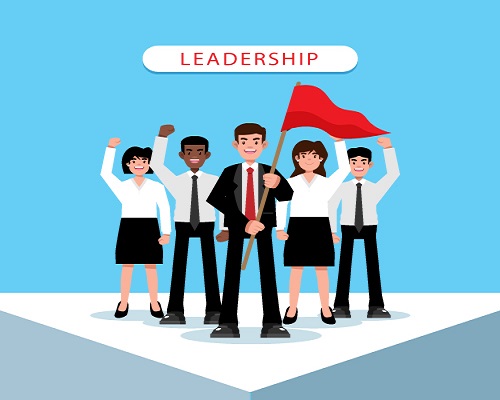
Leadership
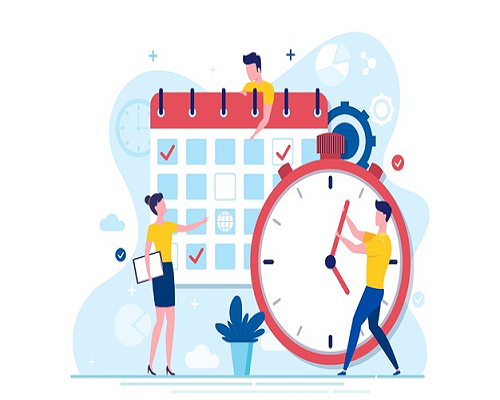
Time Management
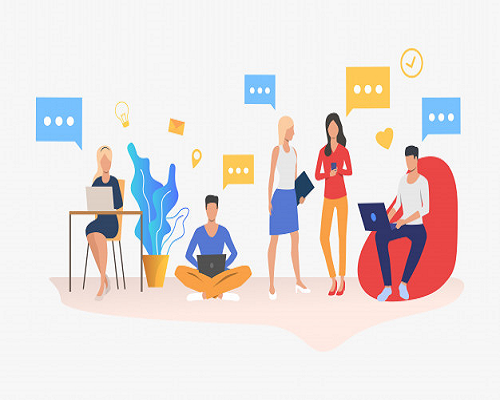
Communication skills
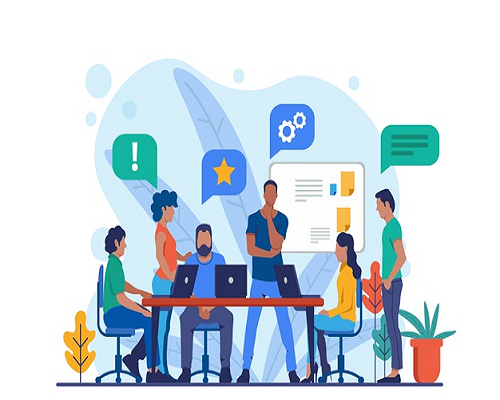
Teamwork
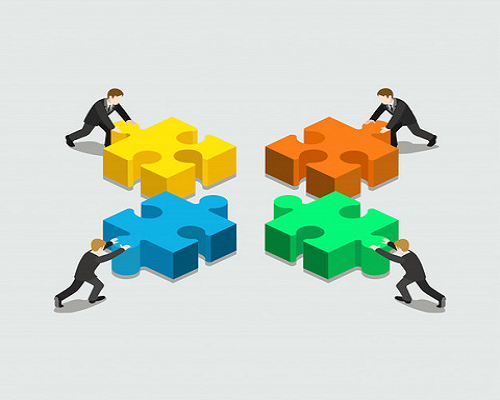